Optimising battery materials
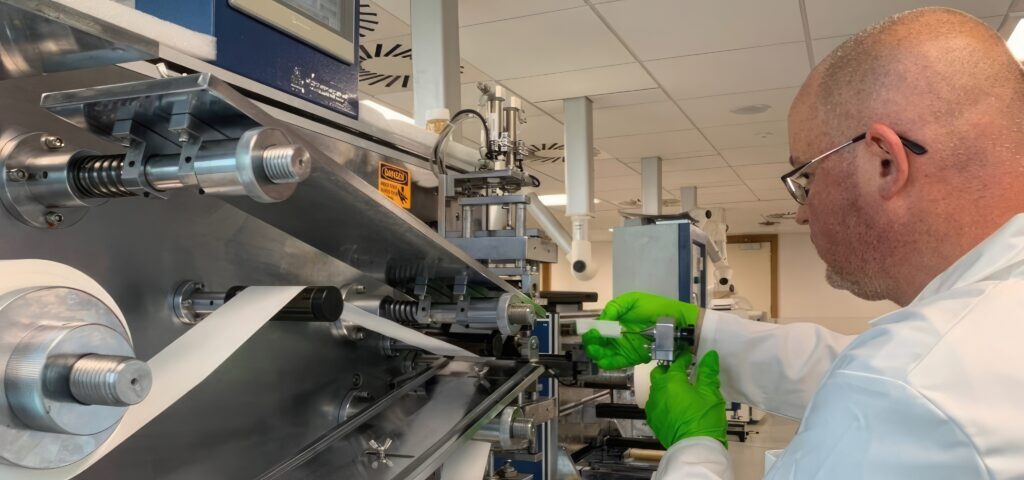
(Courtesy of Nyobol)
Solid state of play
As battery technology moves towards solid-state cells, Nick Flaherty reports on the latest research into improving their performance
There are many materials involved in the optimisation of battery cells beyond the anode, cathode and electrolyte, and researchers around the world are working on a wide range of additives to boost the performance of cells. The move to solid-state cells for example is driving the development of materials ranging from ceramic and polymer layers throughout a cell to materials such as silicon disulphide (SiS2).
The additives, from polymer coatings for electrodes to flame-retardant materials in the electrolyte, are also pointing the way to making lithium metal and lithium sulphur cells more viable, providing a route to cells with much higher energy densities.
Solid-state materials
Researchers in Korea have developed a low-cost SiS2 production technology to boost all-solid-state battery (ASSB) performance.
A team led by Dr Ha Yoon-Cheol, a Principal Researcher in the Next Generation Battery Research Centre at the Korea Electrotechnology Research Institute (KERI), and Dr Cheol-Min Park, a Professor of School of Materials Science and Engineering at Kumoh National Institute of Technology (KIT), have developed the technique for producing SiS2 for argyrodite-type solid-state batteries based on Li6PS5Cl.
They replace the liquid-state electrolytes that transfer ions between the anode and cathode with a solid that is less prone to fire or explosion. However, there remain many challenges to achieve commercialisation such as difficulties in processing and mass production, and high material cost.
Adding SiS2 to solid-state electrolytes for ASSBs helps improve ionic conductivity and moisture stability. The material also helps boost the performance of layered materials with tuneable bandgaps, valley polarisation, and weak van der Waals interlayer forces.
However, the synthesis of SiS2 from sulphur and silicon requires a high reaction temperature, which leads to surges in the vapour pressure of sulphur, making the production of SiS2 particularly tricky. For this reason, SiS2 is very expensive, currently costing about KRW 1.7 million ($1300) for 20 g.
The chemical synthesis process optimises the arrangement of sulphur, silicon and carbon powders in a sealed environment to withstand the vapour pressure of sulphur at 800 ºC. The quality of the resulting product was comparable to commercially available products but with a simpler production process and lower costs.
The SiS2 was fabricated using amorphous carbon in a simple mechanical process. It has a high lithiation/delithiation capacity of 1610/1363 mAh/g; a high initial coulombic efficiency, of 84.7%; extremely high cycling stability after 800 cycles; and a high rate capability.
Furthermore, SiS2 is incorporated into a lithium-argyrodite solid-state electrolyte (SSE) used in ASSBs, resulting in noteworthy air/moisture stability and high ionic conductivity with low activation energy. The researchers say the large-scale synthesis method, exceptionally high lithium storage characteristics, and exceptional SSE application of the layered SiS2 make it highly suitable for various applications.
“Researchers have struggled to address the elevated vapour pressure of sulphur, which required using expensive raw materials or introducing special processes,” says Dr Ha. “What we have achieved will contribute to producing SiS2 for solid-state electrolytes cheaper and easier.”
The team also used SiS2 as an anode active material for liquid electrolyte-based lithium sulphur batteries and identified the destruction and recovery of layered structures during charging and discharging for the first time.
KERI is preparing a patent application for this technology.
Another project, called SOLBAT, in the UK, is developing a deep understanding of the mechanisms behind the premature short-circuiting and failure of solid-state batteries – a crucial step towards avoiding such events and realising the commercial potential of this technology.
For the anode, the project will investigate the use of lithium metal alloys, the nature of the anode/electrolyte interface and the use of lithium-less solid-state batteries as ways to increase critical current densities, improve cycling performance, reduce manufacturing cost and prevent cell failure by managing dendrite growth and void formation.
For the cathode, the researchers are looking at polymers that can be used as a coating between the solid electrolyte and cathode active particles to minimise swelling and reduce cell operating pressures.
Controlling the microstructure and mechanical properties of the solid electrolyte separator can minimise the growth of the dendrites that can cause short-circuits and reduce the thickness of the separator.
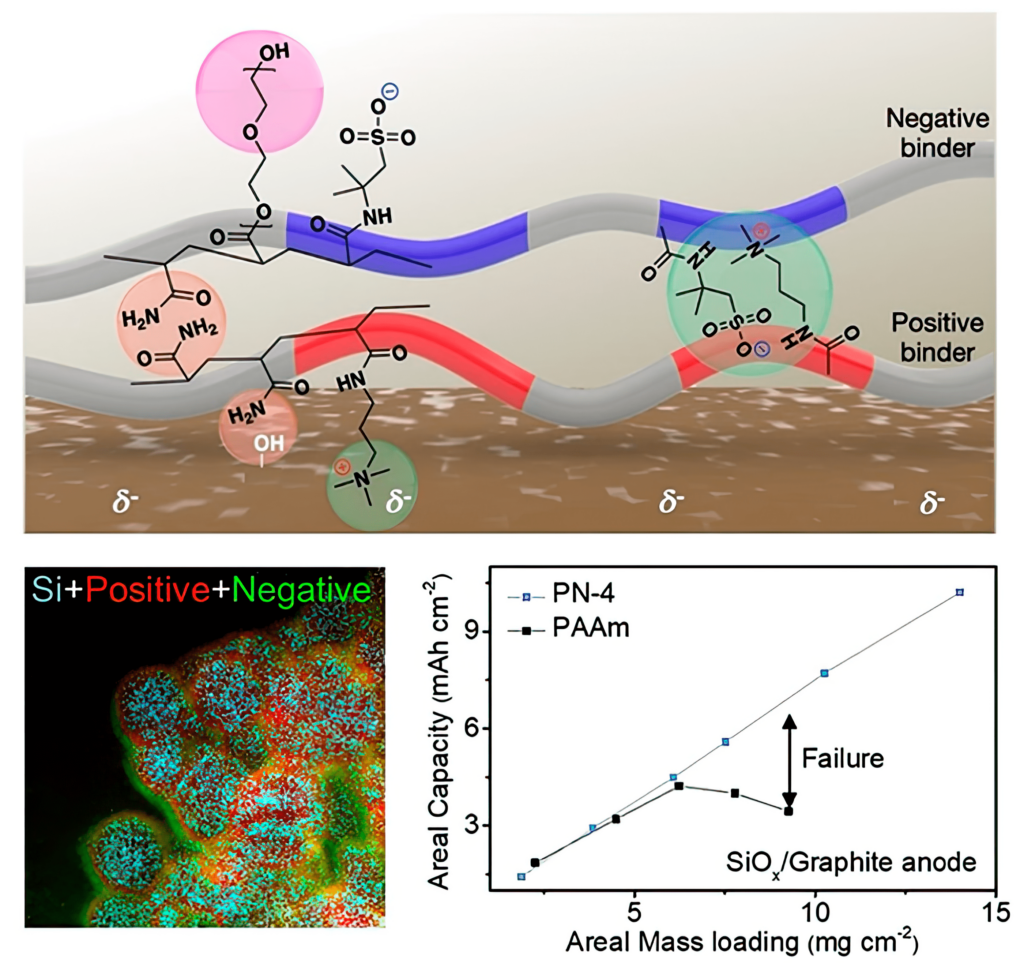
(Courtesy of Postech)
Layered anodes
Researchers from the Pohang University of Science and Technology (Postech) and Sogang University in Korea have developed a functional polymeric binder for a stable, high-capacity anode material that could increase the current EV range by a factor of at least 10.
They produced it by replacing graphite with a silicon anode combined with a layered charged polymer binder to boost stability and reliability. The charged polymeric binder builds a dynamically charge-directed network on the active materials with high versatility, and efficiently dissipates the electrode stress
The polyethylene glycol (PEG) in the charged binder offers a fast lithium-ion conduction pathway that can form an ultra-thick silicon oxide-based electrode (about 10.2 mAh/cm2) without compromising the reversible specific capacity and promote effective charge interaction as a mechanical modulator.
The challenge is that the volume expansion of high-capacity anode materials during the reaction with lithium poses a threat to battery performance and stability. To mitigate this issue, researchers have been investigating polymer binders that can effectively control the volumetric expansion.
Research to date has focused on the chemical cross-linking of the polymer and hydrogen bonding. Chemical cross-linking involves covalent bonding between binder molecules, making them solid but has a flaw: once broken, the bonds cannot be restored. On the other hand, hydrogen bonding is a reversible secondary bonding between molecules based on electro-negativity differences, but its strength (10-65 kJ/mol) is relatively weak.
The polymer developed by the research team uses hydrogen bonding but also takes advantage of Coulombic forces that are the result of the attraction between the positive and negative charges.
These forces have a strength of 250 kJ/mol, much higher than that for hydrogen bonding, yet they are reversible, making it easy to control the swelling of the material. The surface of high-capacity anode materials is mostly negatively charged, and the layering-charged polymers are arrayed alternately with positive and negative charges to effectively bind with the anode.
Introducing PEG to regulate the physical properties and boost the lithium-ion diffusion results in the high-capacity electrode and maximum energy density in a cell.
“The research holds the potential to significantly increase the energy density of lithium-ion batteries by incorporating high-capacity anode materials, thereby extending the driving range of eEVs. Silicon-based anode materials could potentially increase driving range at least tenfold,” said Professor Soojin Park at Postech, who led the work.

(Courtesy of Shinshu University)
Vanadium anode
Researchers in Japan have developed an anode materials that is particularly stable in solid-state battery cells.
The material is Li8/7Ti2/7V4/7O2, a binary system composed of optimised portions of lithium titanate (Li2TiO3) and lithium vanadium dioxide (LiVO2). When milled down to particles nanometres in diameter, it offers a high capacity thanks to its large quantity of lithium ions that can be reversibly inserted and extracted during the charge/discharge process.
Unlike other positive electrode materials, the material has nearly the same volume when fully charged as when fully discharged. That is the result of a fine balance between two independent phenomena that occur when lithium ions are inserted or extracted from the crystal.
The removal of the lithium ions, called delithiation, causes an increase in free volume in the crystal, making it shrink. Some vanadium ions then migrate from their original position to the spaces left behind, acquiring a higher oxidation state in the process. This causes a repulsion with oxygen, which in turn produces an expansion of the crystal lattice.
“When shrinkage and expansion are well-balanced, dimensional stability is retained while the battery is charged or discharged – that is, during cycling,” says Professor Naoaki Yabuuchi of Yokohama National University, who led the work. “We anticipate that a truly dimensionally invariable material – one that retains its volume upon electrochemical cycling – could be developed by further optimising the chemical composition of the electrolyte.”
The research team tested this new positive electrode material in an all-solid-state cell by combining it with a solid electrolyte and a negative electrode. This had a capacity of 300 mAh/g with no degradation over 400 charge/discharge cycles.
“The absence of capacity fading over 400 cycles clearly indicates the superior performance of this material compared with those reported for conventional all-solid-state cells with layered materials,” says Associate Professor Neeraj Sharma from UNSW Sydney, Australia, who also worked on the project. “This finding could drastically reduce battery costs.”
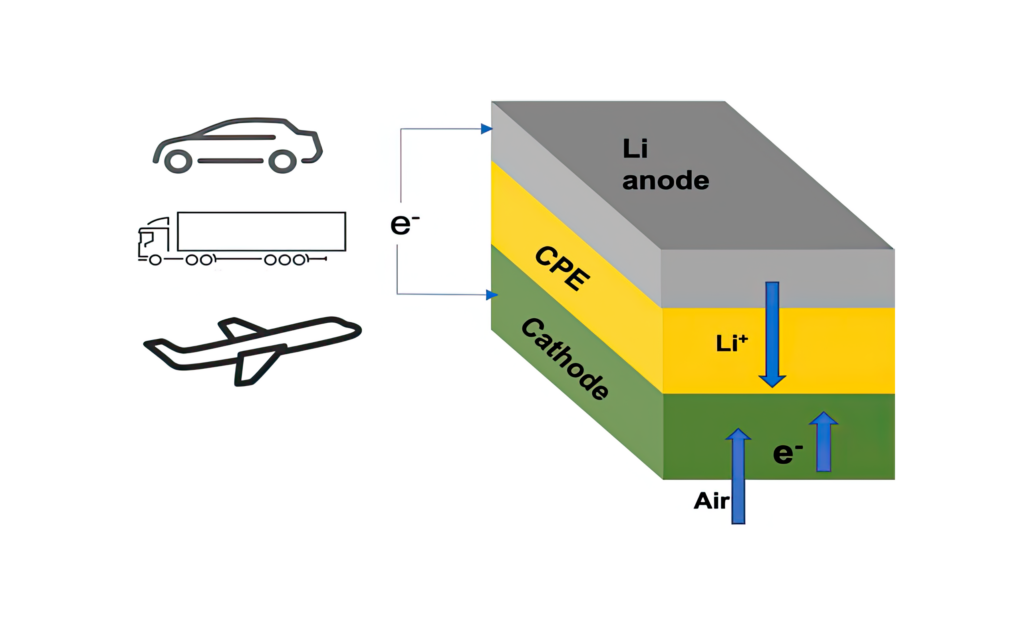
(Courtesy of Argonne National Laboratory)
Solid polymer electrolytes
Lithium metal batteries (LMBs) have the potential to double the amount of energy stored in a single charge compared to current lithium-ion batteries (LIBs), but lithium dendrite growth and electrolyte consumption in current LMB technologies are hindering battery performance.
Substrates for solid polymer electrolytes (SPEs) can help but require optimisation before being used in all-solid-state LMB (ASSLMB) systems.
A team of leading scientists from Shinshu University, Kyoto University and Sungkyunkwan University have therefore used a mechanical pressing method to develop a bi-layer, non-woven polyethylene terephthalate (PET) microfibre/polyvinylidene fluoride (PVDF) nanofibre membrane.
This acts as a separator for LIB systems to prevent short-circuits between electrodes. The separator demonstrated improved wettability (the ability of the lithium ion-containing electrolyte liquid to come into contact with the electrodes) and thermal stability of the battery system.
This bi-layer membrane can also be used in lithium metal batteries to prevent detrimental lithium dendrite growth and structural failure. A similar bi-layer, non-woven PET/PVDF (nPPV) substrate was developed using an electrospinning method to prevent the formation of voids and folds between the two layers that reduce the longevity of the PVDF layer.
The study characterised the nPPV-reinforced solid polymer electrolytes (nPPV-SPEs) for their mechanical, thermal and electrochemical properties. The tests confirmed that the substrate significantly improved the performance of ASSLMB systems.
“Considering that the poor cycling performance of SPEs stems from low mechanical and thermal properties, this project focused on the fabrication of SPEs reinforced by a bi-layer substrate consisting of a layer of PET non-woven fabric and a layer of PVDF nanofibres to improve the structural stability and thus the cycle performance of SPEs,” says Ick Soo Kim, professor at the Nano Fusion Technology Research Group in the Institute for Fibre Engineering (IFES) at Shinshu University.
SPEs made up of polymer matrices and lithium salts demonstrate properties such as flexibility and processability that are compatible with LMB electrodes. The electrospinning method also eliminates the folds and voids generated by the pressing method between the PET and PVDF layers, providing a simple, easy and adaptable manufacturing method for nanofibre membranes.
“The nanofibres produced using industrial scale electrospinning equipment by Lemon Co ensure small and uniform pore size with high porosity, thus accommodating polymeric materials and lithium salts without affecting ion diffusion and improving electrochemical oxidation stability,” said Kim. For this study, PVDF nanofibres were electrospun directly onto the microfibre PET layer to produce a more robust bilayer material. Improved structural stability allows SPEs to bear the chemical reactions occurring in the system during longer-term charging and recharging cycles. “The bilayer substrate significantly improves the mechanical and thermal properties of solid polymer electrolytes, which enables the cell to operate over 2000 hours,” said Kim. The high tensile strength of the material suppresses lithium dendrite growth, one of the significant challenges of LMB systems.
“The improved structure stability of SPEs ensures a long lifespan and safe use of lithium batteries, but the rate performance and lithium mobility of SPEs are still inferior to liquid electrolytes in lithium ion batteries. The next step is improving the ionic conductivity to meet the requirements of fast charge and discharge,” he said.
Substrates for solid polymer electrolytes (SPEs) offer a potential solution to current LMB limitations, but SPEs require their own optimization prior to integration into all-solid-state LMB (ASSLMB) systems.
A team of leading scientists from Shinshu University, Kyoto University and Sungkyunkwan University recently reported the development of a bilayer, nonwoven polyethylene terephthalate (PET) microfibre/polyvinylidene fluoride (PVDF) nanofibre membrane using a mechanical pressing method, which acts as a separator for LIB systems to prevent short circuits between electrodes.
The separator demonstrated improved wettability, or ability of the lithium ion-containing electrolyte liquid to come in contact with the electrodes, and thermal stability of the battery system.
This bilayer membrane can also be used in SPEs of LMB systems to prevent detrimental lithium dendrite growth and structural failure. A similar nonwoven PET/PVDF (nPPV) bilayer substrate was developed using an electrospinning method to prevent the formation of voids and folds between the two layers that reduce the longevity of the PVDF layer. This electrospinning provides a simple, easy and adaptable manufacturing method for nanofibre membranes.
Tests confirmed that the substrate significantly improved the performance of ASSLMB systems.
“Considering the poor cycling performance (charge-discharge cycles) of SPEs stemming from low mechanical and thermal properties, this project focused on the fabrication of SPEs reinforced by a bilayer substrate comprised of a layer of PET nonwoven fabric and a layer of PVDF nanofibres to improve the structural stability and thus the cycle performance of SPEs,” says Ick Soo Kim, professor at the Nano Fusion Technology Research Group in the Institute for Fibre Engineering (IFES) at Shinshu University in Korea.
“The nanofibres produced using industrial-scale electrospinning equipment ensure small and uniform pore size with high porosity, thus accommodating polymeric materials and lithium salts without affecting ion diffusion and improving electrochemical oxidation stability,” he says.
For this study, PVDF nanofibres were electrospun directly onto the microfibre PET layer to produce a more robust b-layer material that support the chemical reactions occurring in the system during longer-term charging and recharging cycles.
“The bi-layer substrate significantly improves the mechanical and thermal properties of solid polymer electrolytes, which enables the cell to operate over 2000 hours,” says Prof Kim. Moreover, the high tensile strength of the material suppresses lithium dendrite growth, one of the major challenges with LMB systems.
However, more work is required to increase the performance of solid-state electrolytes (SSEs) such as SPEs. “The improved structure stability of SPEs ensures a long lifespan and safe use of lithium batteries, but the rate performance and lithium mobility of SPEs are still inferior to liquid electrolytes in lithium-ion batteries,” Prof Kim says. “The next step is to improve the ionic conductivity to meet the requirements of fast charge and discharge.”
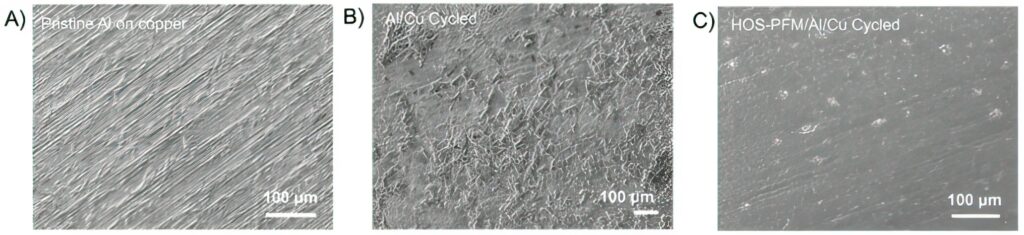
(Courtesy of Berkeley Labs)
Lithium-air SSBs
Researchers at the Illinois Institute of Technology and the US Department of Energy’s Argonne National Laboratory have developed a lithium-air battery using a solid electrolyte that could provide an energy density of 1200 Wh/kg – four times that of today’s batteries.
“The lithium-air battery has the highest projected energy density of any battery technology being considered for the next generation of batteries beyond lithium-ion,” says Larry Curtiss, a Distinguished Fellow at Argonne.
In previous lithium-air designs, the lithium in a lithium metal anode moves through a liquid electrolyte to combine with oxygen during the discharge, yielding lithium peroxide (Li2O2) or superoxide (LiO2) at the cathode. The peroxide/superoxide is then broken back down into its lithium and oxygen components during the charge. This chemical sequence stores and releases energy on demand.
The solid electrolyte is a Li10GeP2S12 ceramic polymer material built from nanoparticles embedded in a modified polyethylene oxide polymer matrix that enables the chemical reactions that produce lithium oxide (Li2O) on discharge.
“The chemical reaction for lithium superoxide or peroxide involves only one or two electrons stored per oxygen molecule, whereas that for lithium oxide involves four electrons,” says Argonne chemist Rachid Amine. This gives the higher theoretical energy density.
The design is the first lithium-air battery to achieve a four-electron reaction at room temperature and with oxygen from ambient air rather than pressurized tanks. To confirm the four-electron discharge operation, the team used transmission electron microscopy of the discharge products on the cathode surface.
Previous lithium-air test cells have also suffered from very short cycle lives. The new design has been tested over 1000 cycles, demonstrating its stability over repeated charging and discharging cycles.
“With further development, we expect our new design for the lithium-air battery to also reach a record energy density of 1200 Wh/kg,” says Curtiss. “That is nearly four times better than lithium-ion batteries.”
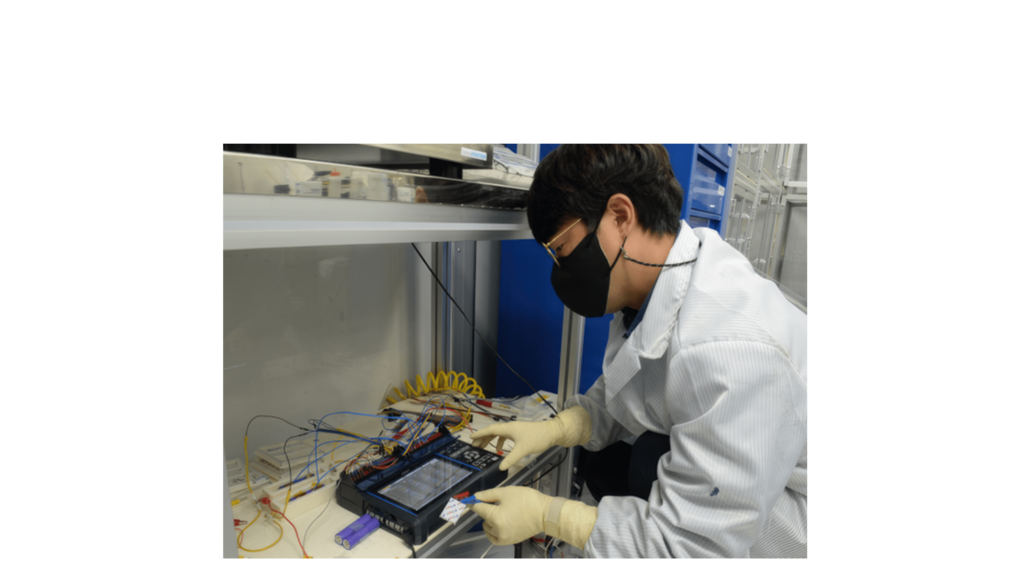
(Courtesy of University of Coventry}
Polymer coatings
Scientists at Lawrence Berkeley National Laboratory have developed a conductive polymer coating for lithium ion cells that conducts electrons and ions at the same time. This ensures battery stability and high charge/discharge rates while enhancing battery life. The coating also shows promise as a battery adhesive that could extend the lifetime of a lithium-ion battery from an average of 10 years to about 15.
Silicon and aluminium are promising electrode materials for lithium-ion batteries because of their potentially high energy storage capacity and lightweight profiles. But these cheap and abundant materials quickly wear down after multiple charge/discharge cycles.
The coating is a conductive binder is made of a non-toxic polymer that transforms at the atomic level in response to heat. At room temperature, alkyl end-chains on the poly (9,9-dioctylfluorene-co-fluorenonecomethylbenzoic ester, PFM) polymer chain limit the movement of lithium ions. However, when heated to about 450 ºC, the alkyl end-chains melt away, creating vacant ‘sticky’ sites that ‘grab’ onto silicon or aluminium materials at the atomic level.
The polymer chains then self-assemble into spaghetti-like strands called hierarchically ordered structures, or HOS. The resulting strands of material, now called HOS-PFM, allow lithium ions to move with the electrons along aligned conductive polymer chains, boosting the energy transfer.
This HOS-PFM polymer was used to coat aluminium and silicon electrodes and tested in a lithium-ion battery set-up. The coating significantly prevents silicon and aluminium-based electrodes from degrading during battery cycling while delivering high battery capacity over 300 cycles with a capacity of 3.0 mAh/cm2.
The HOS-PFM coating could allow the use of electrodes containing as much as 80% silicon, and increase the energy density of lithium-ion batteries by at least 30% as a result.
The team next plans to work with companies to scale up HOS-PFM for mass manufacturing.
Flame-retardant materials
Other materials are aiming to make battery cells more resistant to catching fire, even with a short-circuit.
For example, the Electronics and Telecommunications Research Institute (ETRI) in South Korea has developed a fluorosulphate-based flame retardant additive with significantly improved electrochemical stability, and cell performance compared to triphenyl phosphate (TPP).
TPP is a conventional phosphorous flame retardant; existing phosphate additives have flame-retardant properties but there has to be a large amount of them in the electrolyte. That increases the interfacial resistance (the chemical reaction between the electrolyte and the electrode) which reduces the performance of the battery and its lifetime.
The ETRI team analysed more than 10 types of commercially available phosphorous flame retardants through electrochemical experiments, synthesised a fluorosulphate-based flame-retardant additive for the first time, and improved the shortcomings of conventional phosphorous flame retardants.
The team used the fluorosulphate material in cell with a nickel, manganese, and cobalt cathode (with a nickel content of over 90 %) and a lithium metal anode that is more susceptible to short-circuits and growth of dendrites.
The results showed the flame-retardant properties were improved by 2.3 times, and the performance of the battery by 160%, compared to an electrolyte with a conventional flame retardant additive. The new additive is easy to commercialise, as it can be produced without changing the existing lithium-ion battery production process.
“We wanted to overcome the limitations of exiting flame-retardant additives and realise highly safe lithium-ion batteries through this research,” says Jimin Oh, a senior researcher at the Intelligent Sensor Lab at ETRI. “In the future, we will make efforts to contribute to the commercialisation of fluorosulphate-based flame-retardant additive for EV cells.”
The next stage is to apply a flame-retardant additive to anodes using lithium metal oxide anodes and lithium metal cathodes, as well as cells with silicon cathodes.
Conclusion
New additive materials and coatings are boosting the performance and lifetime of different types of battery cells. The ceramic and polymer layers in solid-state batteries are allowing lithium metal to be used safely to boost the energy density. More effective flame retardant materials mean the same safety levels can be achieved with less material, allowing more electrolyte to be used to boost the performance of the cells.
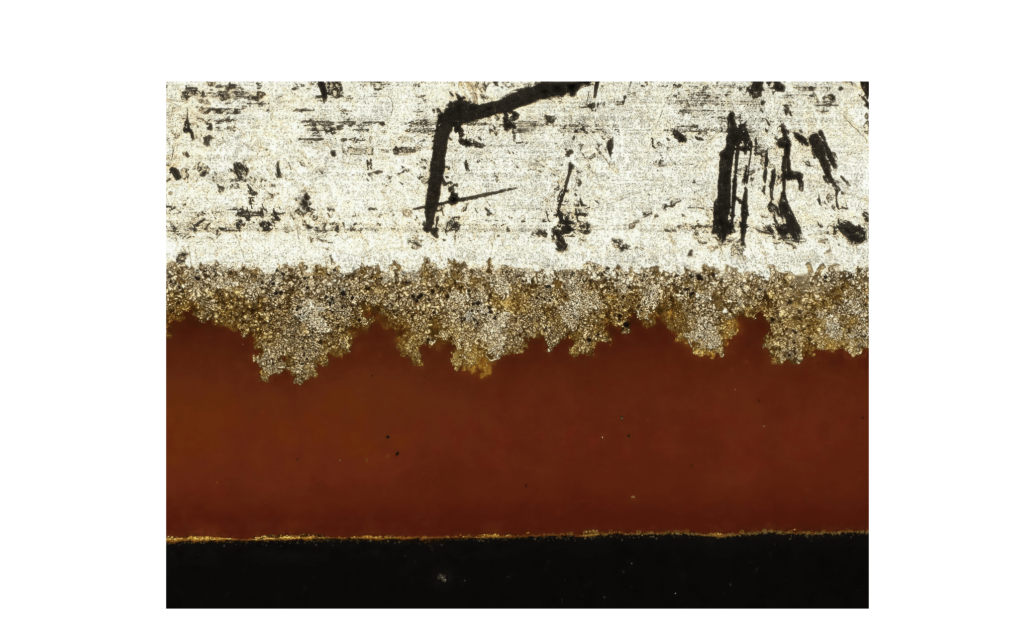
(Courtesy of University of Coventry)
Lithium sulphur
Lithium sulphur (LiS) batteries can provide a lighter option for short-haul aircraft and light goods vehicles in particular, with energy densities of 400-600 Wh/kg, but finding the right combination of materials is still a challenge.
The Listar research project, led by University College London and involving the universities of Birmingham, Cambridge, Coventry, Imperial College London, Nottingham, Oxford, Southampton and Surrey, is therefore looking at the best-performing materials for LiS cells.
“This work is important, because understanding what is happening inside a LiS battery is harder than with lithium-ion,” says Dr Daniel Auger at Cranfield University, which is developing simulations to model the behaviour of the battery in particular vehicle types.
“There is just the one stage of electrochemical processes in lithium-ion, but four in LiS,” he says. “The charge is also very ‘flat’, meaning there are regions of the battery where it is very difficult to ‘see’ the charge. We have to look for different kinds of indicators of what’s happening.”
The project is developing a LiS pouch cells using the most promising anode, cathode and electrolyte components previously tested individually in coin cells.
It will investigate the cathode-electrolyte interfaces of quasi-solid-state batteries with Oxlid in Oxford. It is also developing a solid-state composite cathode for an all-solid-state LiS battery.
ONLINE PARTNERS
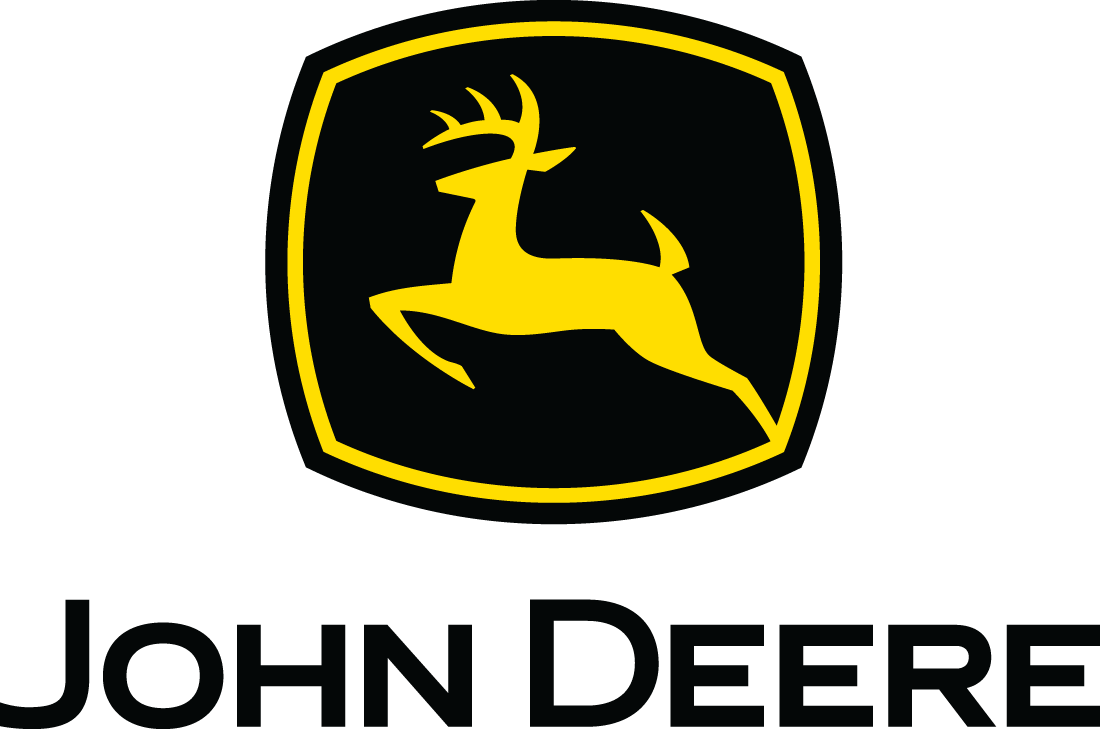
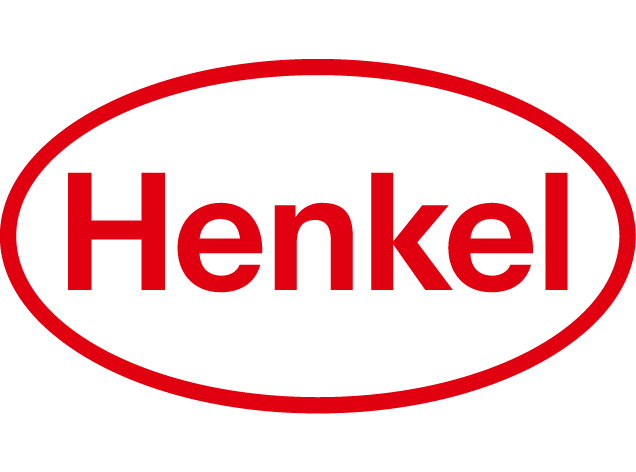
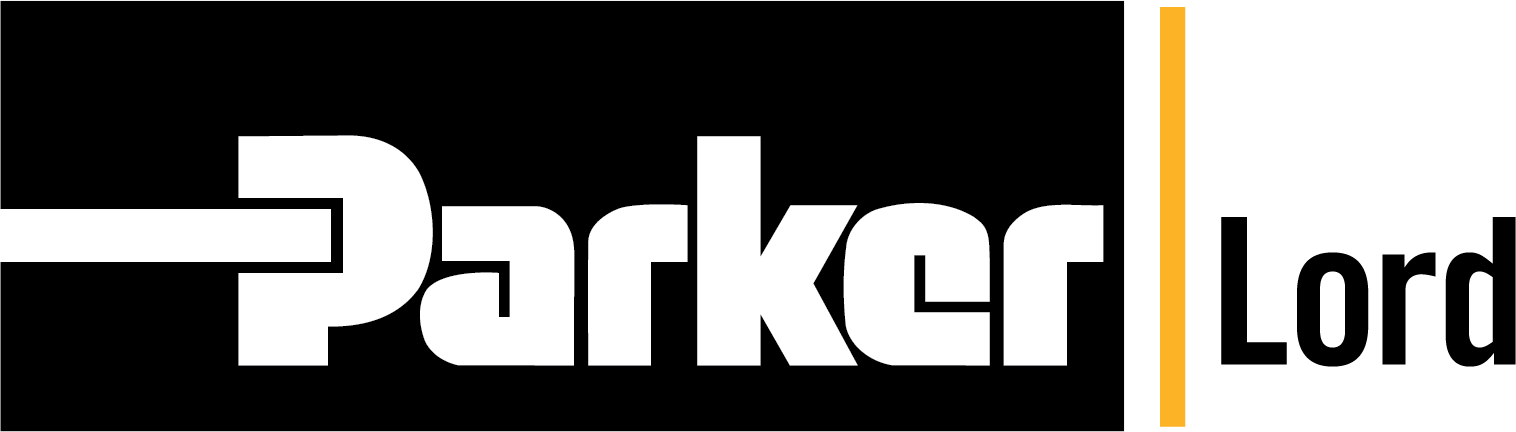
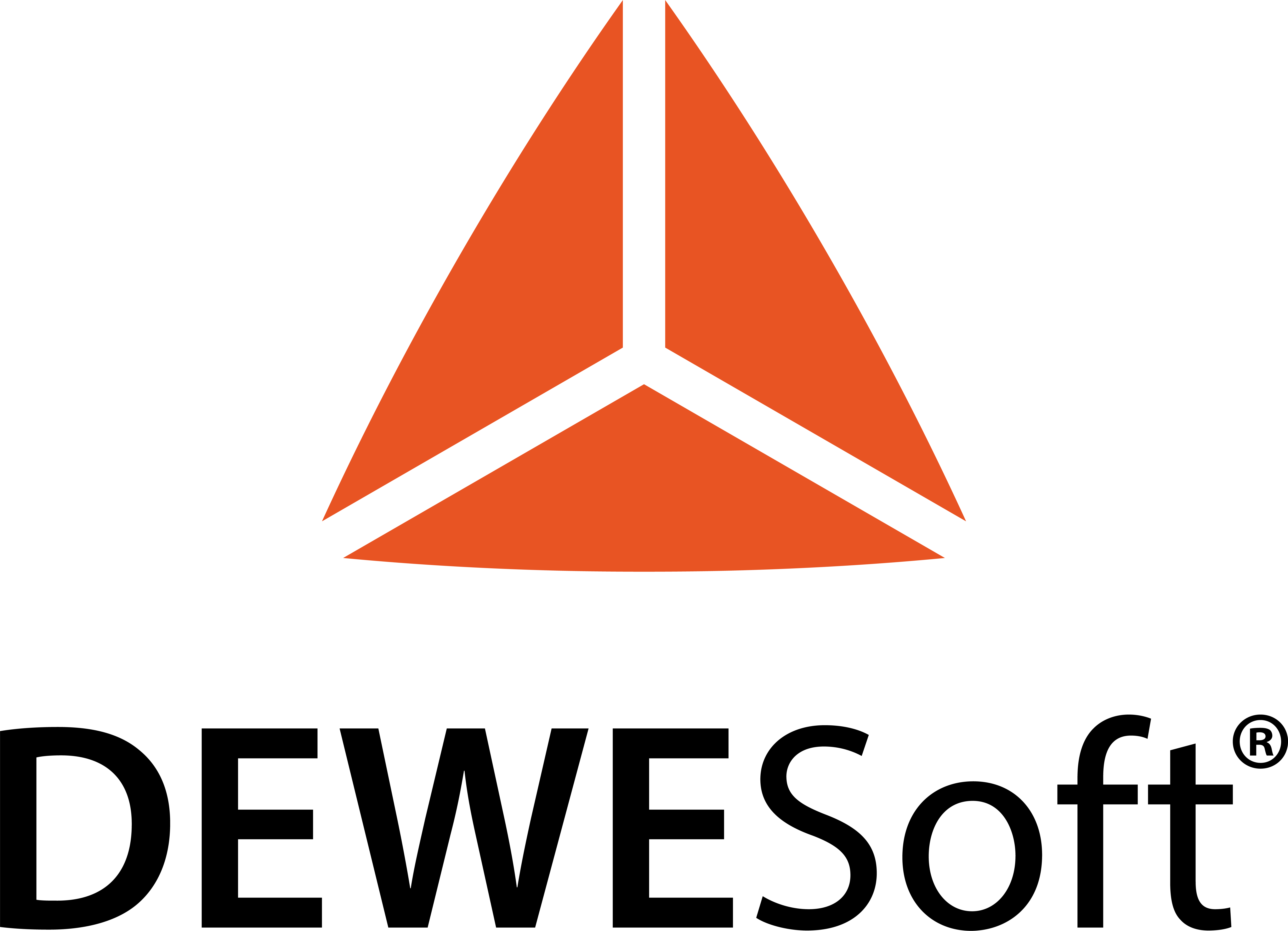
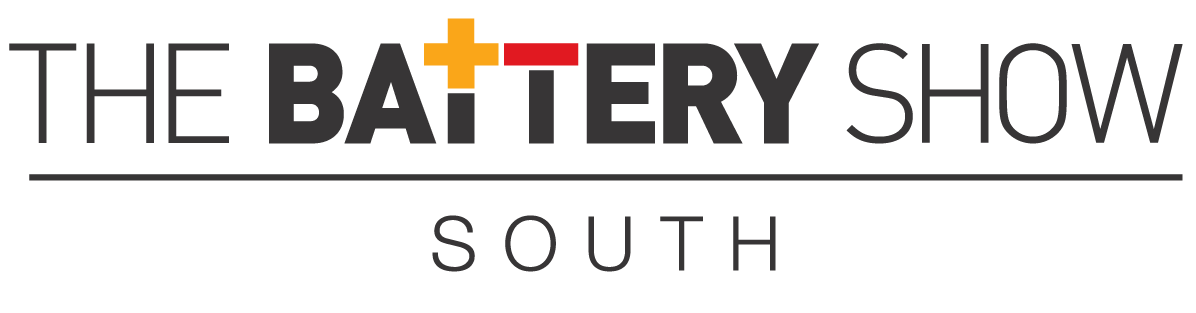
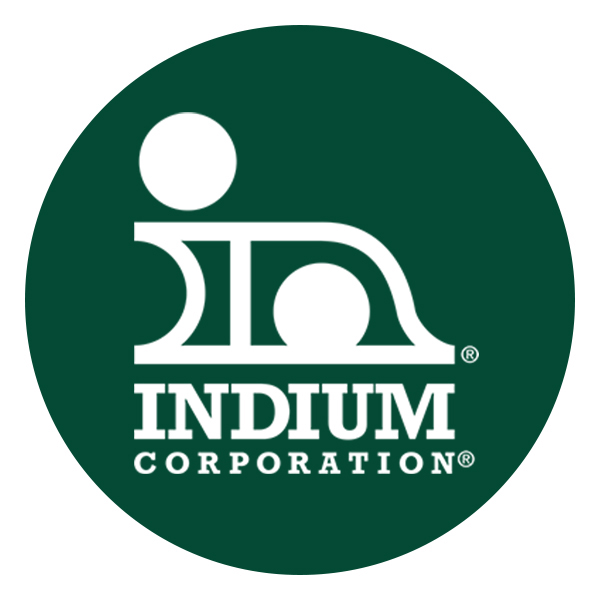

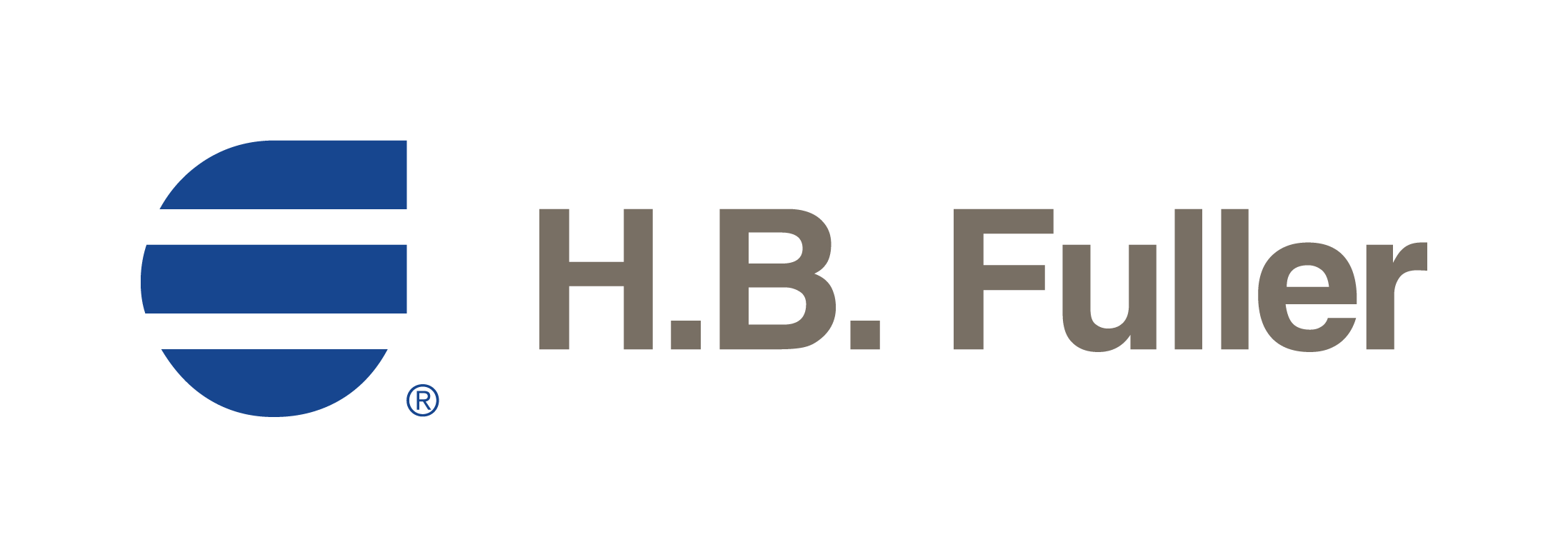
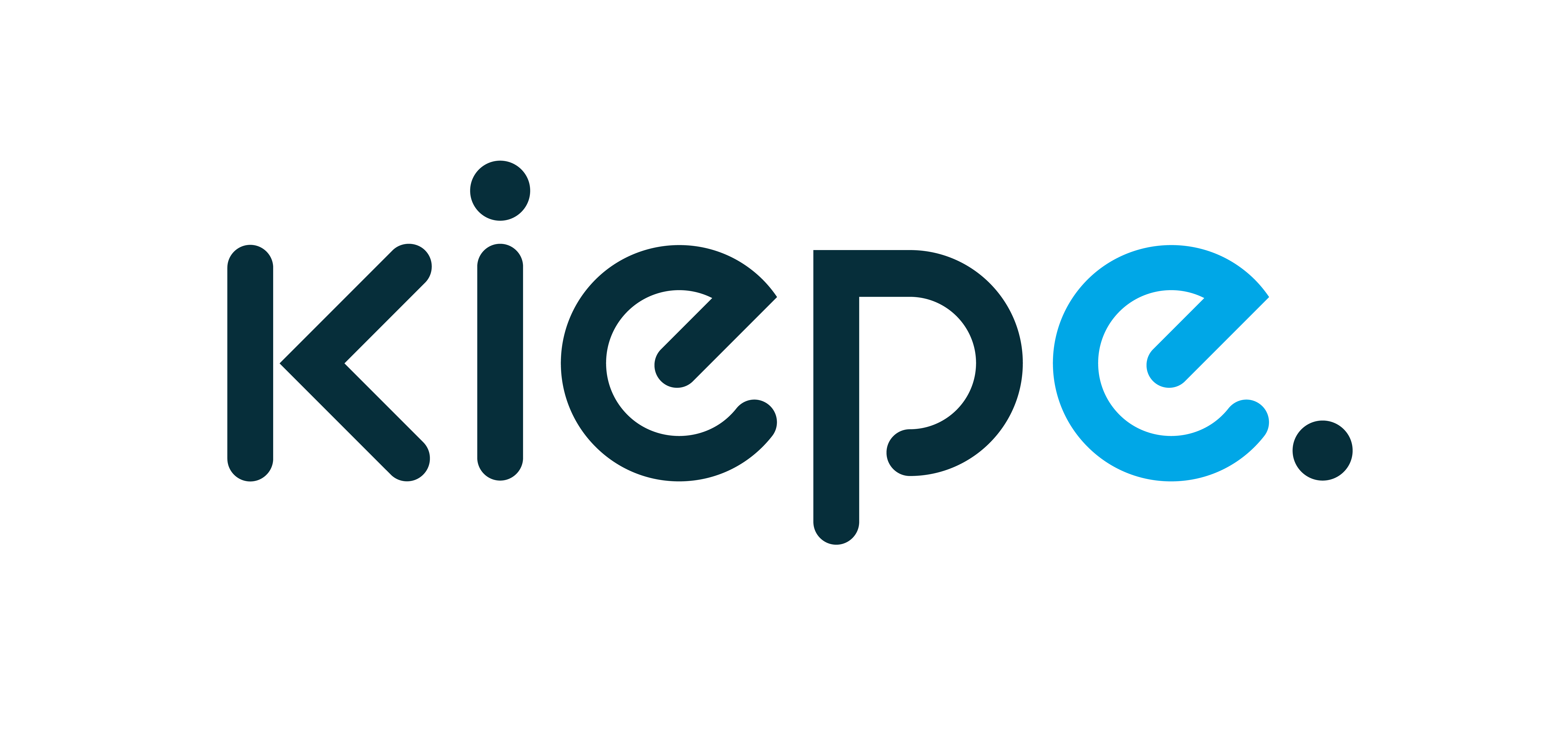
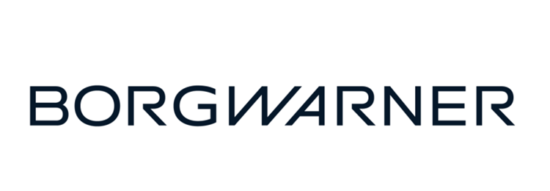