Battery case materials
Housing projects
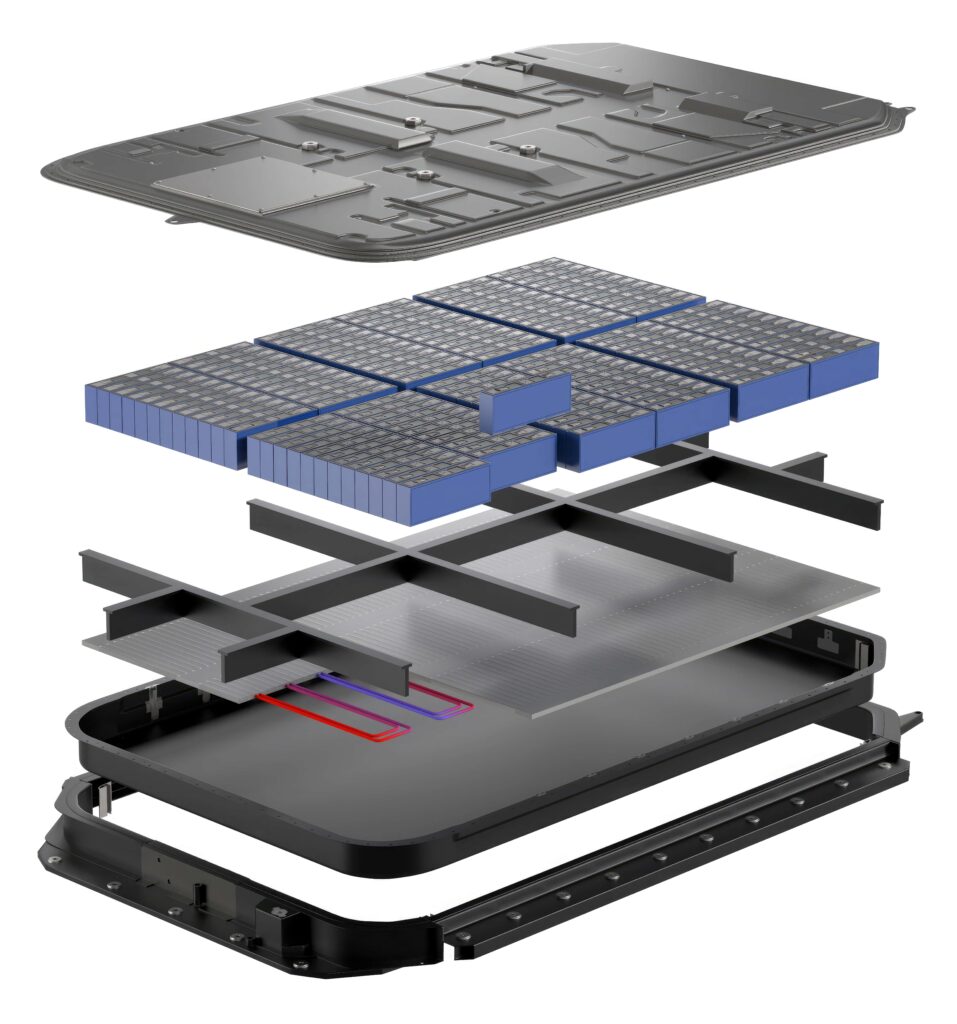
(Courtesy of Henkel)
Battery case designers have a wider than ever choice of materials for enhancing the attributes of their products, reports Nick Flaherty
The range of materials for developing EV battery cases is growing, and are addressing issues of weight, assembly and even condensation. Glass fibre and composites are opening up design options from modular systems to complete cases, while other materials are helping to improve the properties of the cases, from thermal and electrical shielding to collecting the moisture that can cause corrosion.
Using plastics for a battery case can reduce the number of components required by using larger components, which also makes the assembly process more efficient. That also opens up new design approaches for modular cases.
Compared to conventional case designs using traditional materials such as aluminium and other metals, lightweight thermoplastics can potentially provide 30-50% weight savings per component, improve energy density, simplify the assembly process and improve thermal control and safety and enhance crashworthiness.
This marks a major shift in automotive production but requires the entire supply chain to work together. Several large battery enclosures, moulded with its thermoplastics, are expected to be used in production vehicles as early as 2024. One plug-in hybrid EV built in China is already using a thermoplastic polypropylene compound instead of aluminium for its battery case cover, providing savings in weight.
Other EVs now in production around world are using several thermoplastic materials for components such as cell carriers and housings, battery modules and battery enclosures. This requires changes to large-component manufacturing, joining and assembly, crashworthiness, battery thermal management, flame retardancy, electrical properties and performance testing.
One issue with using thermoplastics has been the structural considerations. Designers are increasingly looking at using the battery cells as part of the structure of a vehicle, which means there can be less structural pressure on the design of the case as the cells and modules take more of the stress. But that is also putting more pressure on the adhesive foams used to secure the cell modules to provide more strength as well as thermal conductivity.
Flammability
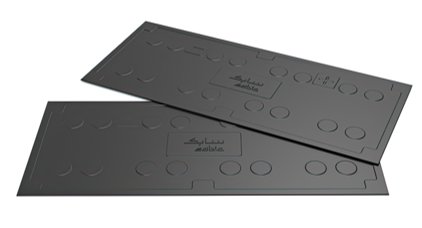
(Courtesy of SABIC)
Flammability is of course a major consideration for the material choice for a battery case, although that is already an issue with bonded aluminium plates and even with steel, which can have challenges with resisting the high temperatures that can occur in a thermal runaway.
The key standard is the UL94 V-0 flammability rating of plastic materials, which is now harmonised with the IEC 60695-11-10 and 60695-11-20 standards and ISO 9772 and 9773. These determine the tendency of a plastic material to extinguish or spread the flame once the sample has been ignited. The V0 rating stops the burning of the material within 10 seconds.
However, version 3 of Regulation 100 in the Automotive Regulatory Guide also specifies a minimum warning to passengers in a vehicle of the risk of a fire in the case. This is not a new challenge: for every EV fire there are 63 fires in vehicles with IC engines. However, the materials in the case are the key to meeting this regulatory standard to give passengers sufficient warning in the unlikely event of a thermal runaway and a fire in the vehicle.
One perception is that plastics are not suitable for battery packs as they cannot prevent thermal runaway and fires. However in testing, an aluminium plate was exposed for 5 minutes to a flame with a temperature of 1100 ºC. The same test on a plate made from long glass fibre polypropylene and a flame retardant (FR) resin reacted very differently. The flame burned through the aluminium in 2.5 minutes, while the glass fibre plate with FR withstood the temperature for the full 5 minutes with no breakthrough.
The work on vehicle electrification technologies extends beyond simply pairing materials to individual components in existing designs. The complete EV battery system and vehicle structure has to be taken into account to identify the right material in the right place, For the case, that means using the properties and strengths of thermoplastics to improve performance, reduce costs and weight, and support mass production.
This includes integrating individual batteries into pouch cells placed within a thin-walled housing moulded with a 30% glass fibre-filled, FR polypropylene compound.
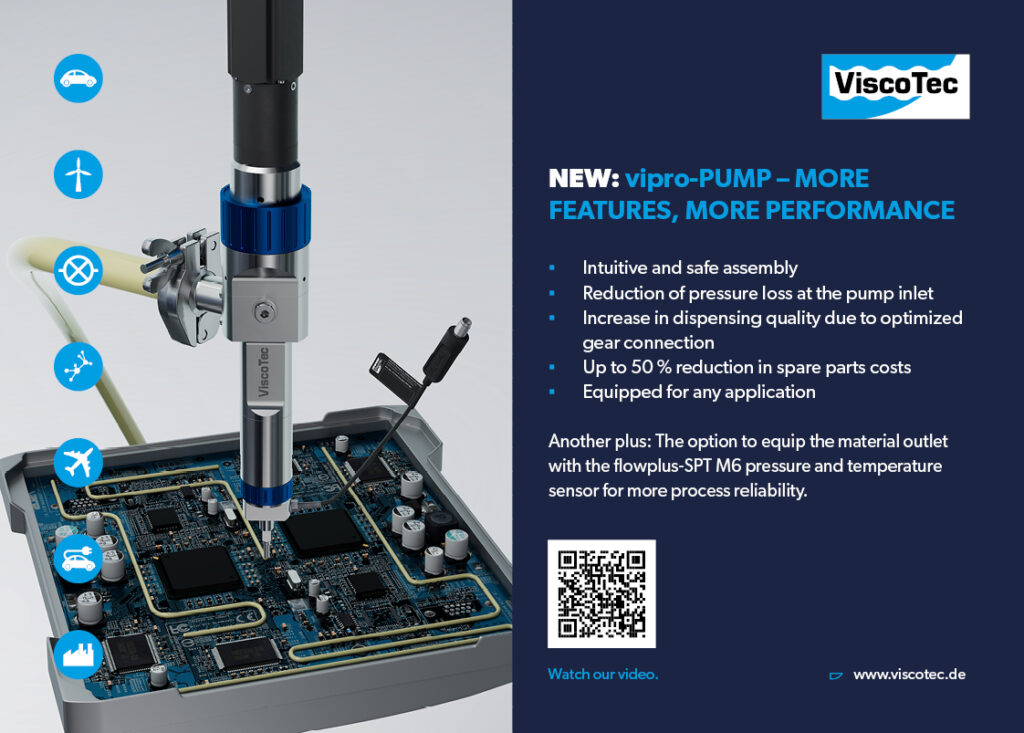
Using plastic also allows different geometric features such as a double-wall construction and new rib patterns to be used that can reduce the weight of the case while meeting the structural requirements.
One alternative that has been used to increase the thermal protection is to use large mica sheets. However these are brittle and are more difficult to source and work with. This is getting more relevant for battery safety. The spray process is also conformable to follow the contours of the top plate. The adhesion of the material on the different substrates, particularly on how the coating behaves with different composites, is also being explored.
Coating technology can be applied on the inner side of the battery lid for a thermal event to protect passengers. This is a liquid coating, water or epoxy based, that is sprayed onto the lid of the battery case. This is sprayed on with a 1-4mm coating thickness and a flat streaming process has been developed for a fast application rate. The spray head was developed with manufacturing partners to be added to equipment.
Thermal conductivity
Thermal gap filler materials are used to fill gaps in the battery case, but there are now more requirements on their structural properties and to provide high thermal conductivity. The thermal requirements are calculated at the module level but the case filler is calculated at the case level.
With cell-to-case designs that are in direct contact with the cooling plate there is no filler; the thermal path is between the cell and the cooling plate. Then there is foam or potting that is structural with the adhesive including an FR additive. This has higher structural properties with low density to minimise the weight by using polyurethane material. Some customers are looking only for structural strength, some require the structural strength with FR properties but both need a high application rate.
As this approach is a new development, battery architecture designers are still looking for the right way to go. With thermal propagation, there is the question of whether the flame retardant needs to be added to the foam or if another technology should be used. For example, foam potting is used for cylindrical cells, while for prismatic and pouch cells fire protection pads or compression pads are used to compensate for swelling.
This provides flexibility in the foam for movement and swelling, but this needs fast curing with one application rather than application in layers. The initial curing has to take only a few minutes to allow for additional processes, while the full curing process needs a full day.
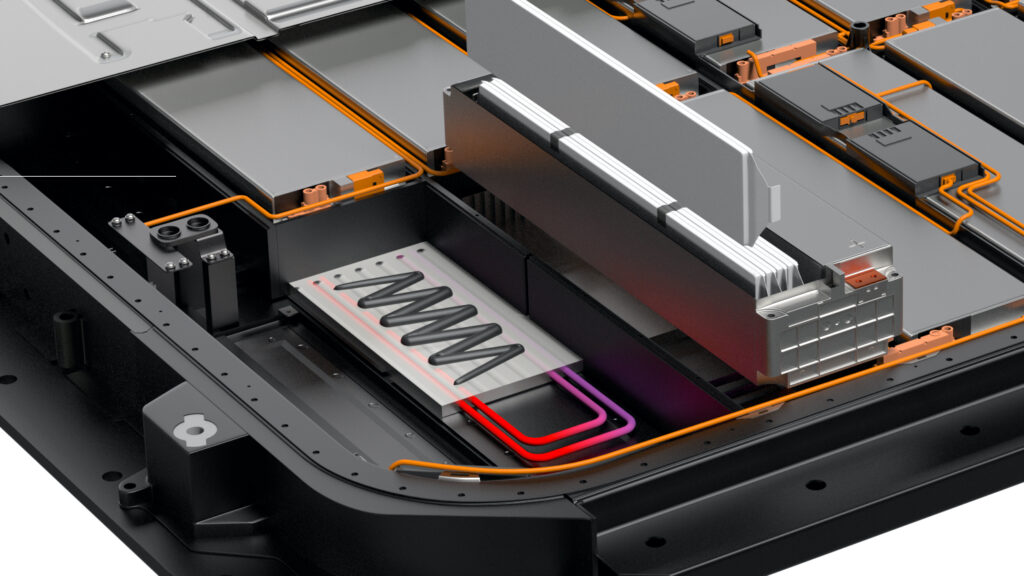
(Courtesy of Henkel)
Recycling
Two sides to the materials question are emerging. There’s the performance and cost of the battery case now, and the recycling issues at the end of the vehicle life in 20 years’ time. Designers want to be certain that the cases can be recycled effectively.
One design assumption for the cases is that at the end of the 20 years, the recycling processes will not be energy-intensive, but the worst case is that the cases will have to be shredded for recycling. That means the main consideration is the combination of adhesives and materials, as their interaction can cause problems in that shredding process.
For example, composites such as carbon fibre-reinforced plastic are difficult to shred. Discontinuous carbon fibre and recycled carbon fibre, might be easier for recycling and can replace structural and non-structural components to replace plastic components in automotive designs, but they are not cost-effective for case designs.
So the design of the case means considering how to take the case apart, and not using materials that are hard to recycle while still ensuring safe performance.
In a modular case, most of the materials are set in the battery platform. These include the plastic carriers, the adhesives and the busbars, all with a UL94 rating of V-0.
The battery case casing is part of the vehicle integration, so each vehicle designer comes with different needs. The case can be highly structural or not at all, the weight can be the top priority or perhaps range is more critical. Modular battery case designs with thermoplastics can provide an increase in energy density of more than 30% versus other designs, as this approach makes optimum use of the space available.
There are several opportunities with a modular design to stop thermal runaway propagation (TRP) before the case casing has to contain it. Ideally, thermal runaway can be prevented at the cell level, then at a group of cells, then a bigger group of cells.
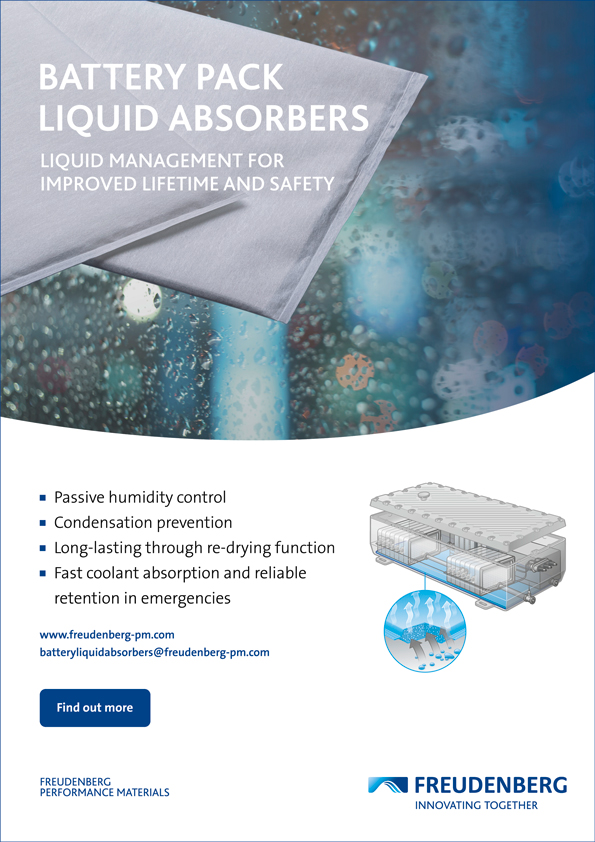
There are several barriers to preventing propagation before it reaches the casing. This is part of the Failure Modes and Effects Analysis, but so far it has not been the critical decider for material choice. Regulation 100.3 in the Automotive Regulatory Guide requires giving occupants a 5-minute warning before there is fire outside the battery case, so the aim is to prevent getting to that point. This requires looking at engineering the materials choices and the gas venting path.
There is a major challenge for battery cases for low-volume automotive platforms, which are difficult to electrify as it is not cost-effective to create a cell-to-case design by creating a brand new cell. The best use of space has to be achieved in other ways, and the modular approach allows the modules to be as big as possible within that space.
The load case is built into the design of the case platform, maximising the size of the module. This minimises the weight by optimising the design at the module level rather than by the choice of material, and allows the use of composites to increase the overall energy density.
For example, using a modular approach allows six aluminium modules to be replaced with one large module made from a non-metallic material. The only metal in the module is used for the cooling plate.
The platform builds in layers of protection for all the potential problems, whether it is water build-up or channelling vent gases which is very much down to the choice of material. If there is a catastrophic cell failure the materials need to channel the gases away from the other cells, to minimise temperature increases in other cells.
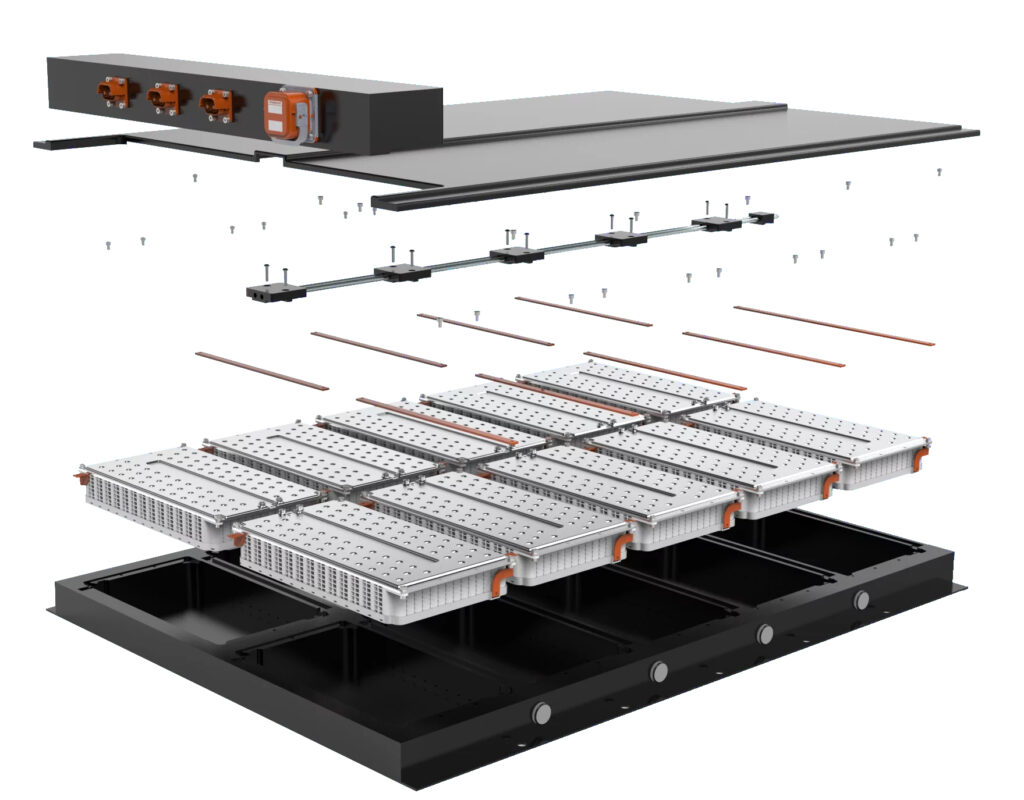
(Courtesy of Ionetic)
De-bondable technology
For sustainable and reusable battery cases there is also work on de-bondable adhesives the cells or modules. At the module level it could help to de-bond a complete module, but that is still challenging as it needs to have a certain design to make it repairable, so it needs a frame in the case.
De-bonding on demand uses an external factor such as current, heat, chemical soaking or even mechanical force to separate the modules or cells from the case. Still under development, that uses an additional layer that can be triggered to remove the adhesion. It is not yet decided which is the right way to go, as the trigger needs to be designed into the case, and it could use printed layers that can provide heating for de-bonding, for example.
The need to disassemble cases is driving more interest in sealant gaskets, so there is an identified need for foam-cast gaskets to rework the case. These are also under development.
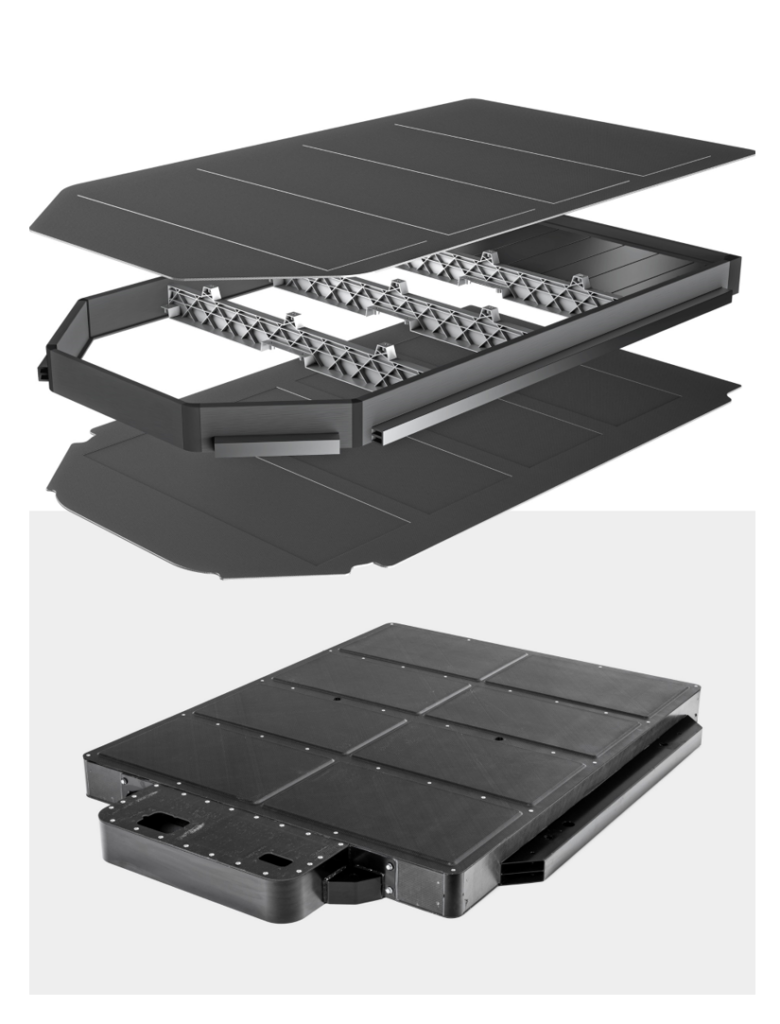
(Courtesy of SGL Carbon)
Testing
Glass fibre top covers, bottom covers and impact protection plates can provide a more cost-effective material for battery cases. The most challenging factor is TRP, as the combustion needs to be contained in the box.
Then there are EMI, thermal and electrical isolation and mechanical issues of drive loads, crashes and impacts to consider. Leak tightness is another important factor, and this is very much a benefit for composite materials such as glass fibre as the case can be a single components without seams and potential leakage points.
EMI considerations need to include a metallic or carbon fibre layer for shielding, so glass fibre can be used with a foil and stack layers via a cost-effective press-moulded process.
With composites, the top and bottom cover can be a flat sheet formed by compression moulding. For the side walls a lot of designs rely on extrusion and pultrusion; for composites the top and bottom covers are most suited to the glass fibre, as elongation and strength are key mechanical considerations.
For even more stiffness, carbon fibre can be more appropriate but that has a price premium, although there are applications for carbon fibre bottom plates for ultra-high end hypercars.
Thermoset materials are used for cost considerations, and use compression moulding with a dry textile and resin applied on top. This has a short cycle time. Prepreg glass fibre is typically more expensive.
Continuous fibre is needed for the underbody covers, while for the top cover shorter fibres can be used with sheet moulding if complex shapes are to be produced that cannot be easily draped from continuous fibre textiles. This is not as easy on the mechanical design and has thermal complications. For example internal pressure from thermal issues in the box can put a mechanical load on the structure, so it needs a thicker wall.
Depending on the load cases, typical wall thickness of a cover starts at a minimum of around 2 mm and as heavy a textile as possible is used to minimise the number of layers, leading to applications with over 3 mm wall thickness, which is only two layers of fabric. However, the thicker material limits the draping properties of the material for creating certain geometric shapes.
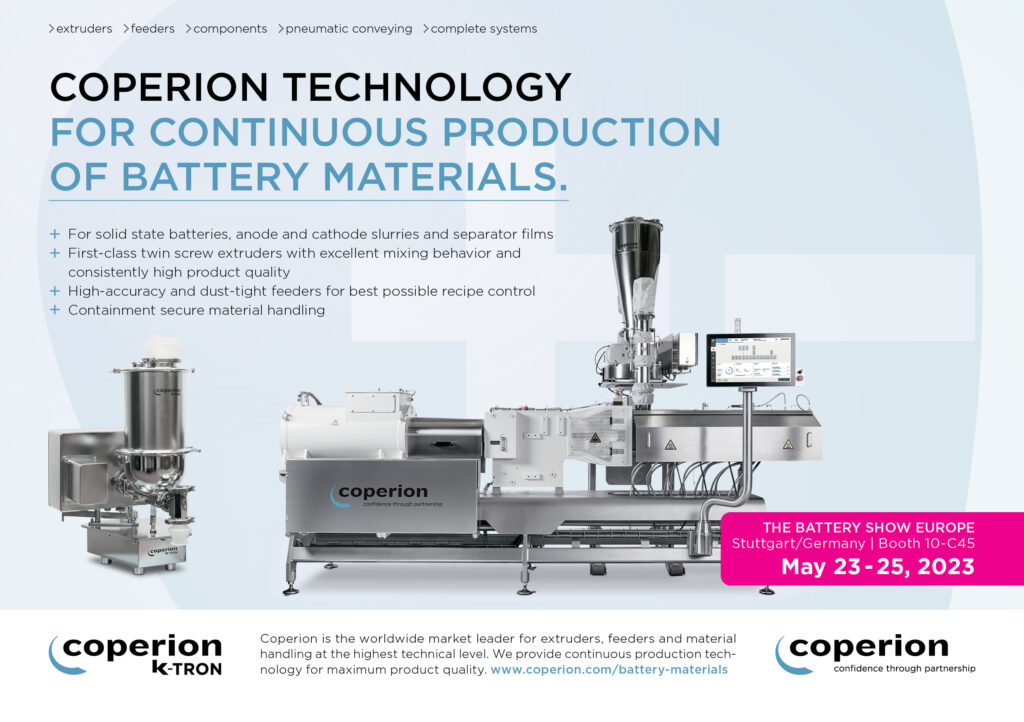
Battery cases used as part of the chassis is an opportunity for composites, as designers need to close off the case with the top and bottom covers. This is good for torsional stiffness of car body. Then there is the side impact load case, which needs to transfer the load across the side rails.
Thermal propagation is the factor that often drives the design, so the covering plate needs to be rigid and thick enough to withstand the thermal propagation.. Plastics are now competing with aluminium, which will not be able to contain a battery fire in the latest test regimes.
Also, steel gets hot very quickly so it needs additional insulation, meaning that the final design is not so thin and not so cheap. That’s the big advantage of composites in isolating the thermal characteristics of the case.
With compression moulding there are limits on geometries from the draping of the material, so there are trade-offs. Injection moulding on the thermoplastic side or sheet moulding compounds on the thermoset side have more flexibility in design but both need more costly tools and bigger machines.
The interesting thing is that there is no one design that is the way forward. A big portion of the market can be addressed with continuous fibre thermoset.
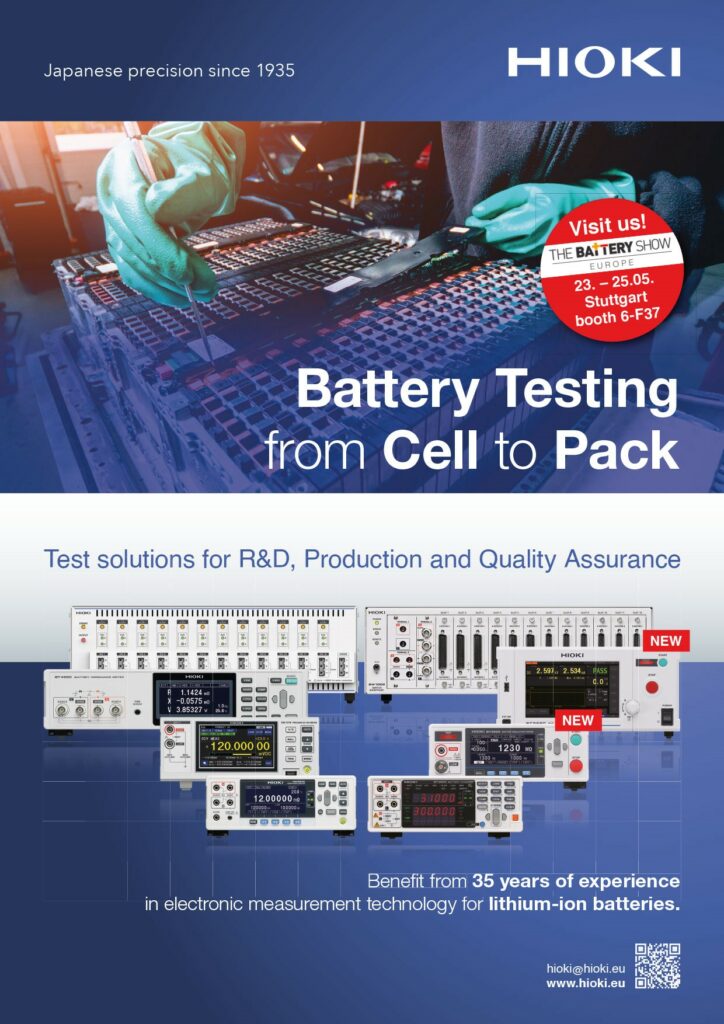
The bottom panel is mostly flat and easily meets the impact requirements. An epoxy resin with flame retardants in the resin is typically used. Phenolic resins are interesting as they do not burn as easily as other resins, and are working well in testing, but the choice depends on the customer requirements
The technology is evolving rapidly, and internal testing for impact and temperature performance is key. This testing showed thicker composite materials than expected are required for the battery pack, and although this can take up more space compared to metal it is still lighter.
Initial tests have focused on a single battery cell in a box, but this is now moving to testing a pressure tight box with 25 large cells in the 21700 form factor. This is similar to the UL2596 standard test, although that uses the smaller 18650 cells.
The testing needs to include temperature testing on the surface at the same time as testing the mechanical loads. A cell fire moves through the box to produce a short-lived high local temperature in different locations and lower-temperature burning throughout the case for a longer duration. A case design needs to cope with both requirements, and have the mechanical strength to handle pressure build-up and particles from cell explosion.
A bigger panel for a larger case with bigger cells also bends more under pressure, and current tests are showing how a material performs with bigger panels.
The next step of a test system is then a full-scale case test. There is lot of differences in the type of textile and the wall thickness of the whole case, as the resin system has an influence on the performance, as does the fibre length.
The test systems are now focusing on impact protection. There is a lot of difference in the requirements of the OEMs, and there are generally two typical scenarios – a small object at high speed, and a larger object with lower velocity hitting the bottom plate. However, the exact energy levels are different for all the platforms. This leads to load cases with a big object at low velocity at 90º, and a small object at high speed at another angle.
Development work is looking at ways to compare big drop tests to smaller lab tests and still get a reliable result. This is important, as testing big panels with a big tower requires a test institute, which is costly and takes up considerable time to do the testing. Matching lab tests to the large-scale performance of a material gives designers more flexibility for case development.
The test conditions are also simulated and matched against the test results using tools such as LSDyna and/or Abaqus. Vehicle designers also do their own simulation and integrate the simulation models of the materials into larger crash models of the car.
Water and humidity
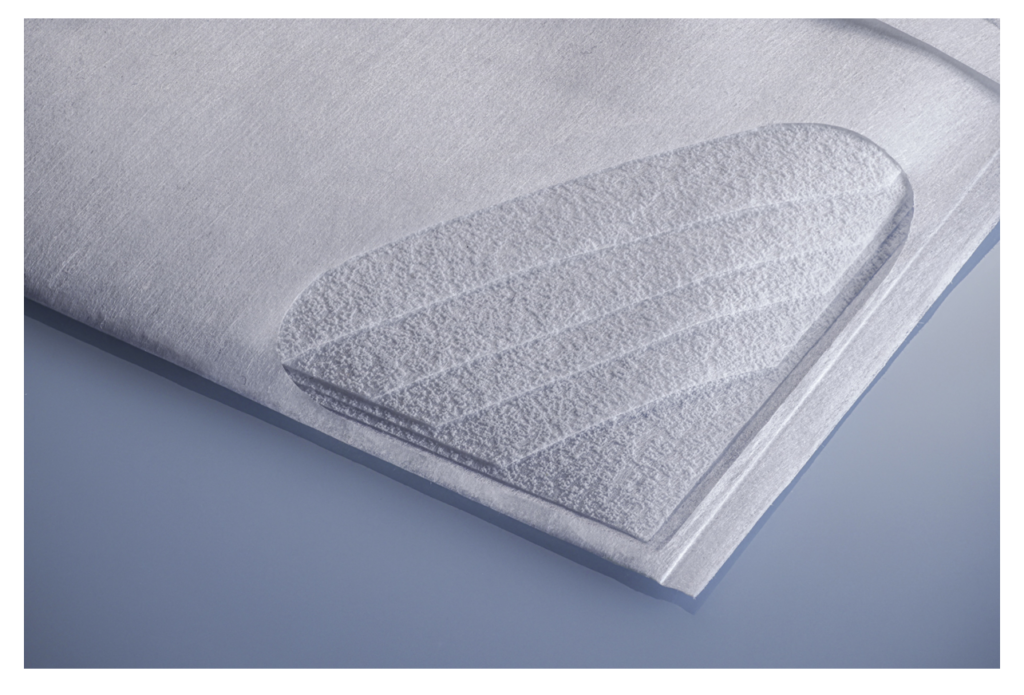
(Courtesy of Freudenberg)
There is a growing demand for materials to address liquid absorption in a battery case. Most engineers are not really aware of this issue and those of corrosion that are already appearing in cases. While this is driving the use of composite materials, it is also driving the adoption of absorbent materials, as some engineers are not aware that the membranes they use allow water vapour to go through and can build up on the cooling plate, leading to corrosion.
Water from the air is only one source though. One case design had an issue with the cooling system, and the developers were worried about a breakage in the cooling system and looking for a material to absorb the glycol coolant.
That project did not progress but it led to a project that needed to maintain a 15-40 ºC temperature range with coolant while making sure there was no leakage. This was achieved with a non-woven material coated with superabsorbent particles. Depending on the humidity outside, the material becomes soft and so absorbs more water.
Tests showed liquid absorbers can manage the humidity in a case by absorbing moisture and releasing it by drying it in a less humid environment.
The standard alternative material for absorbing water in a battery pack is silica gel. This dries the air but is hydroscopic, so there is a diffusion of humidity and it does not redry. It needs a temperature of 80 ºC or humidity below 20% to release the captured moisture. Silica gel also needs to be replaced about every 2 years as part of the regular inspection cycle of a vehicle.

Instead, the non-woven material is not just drying the case but managing the climate, and does not need regular replacement. Tests with 50 climate cycles from +80 to -40 ºC and +80% humidity to 0 did not see any ageing, indicating a suitable lifetime.
The material is also flat, rather than packets of silica that need space in the case, and so can be layered in the centre of the material using an organic superabsorbent polymer (SAP) that coats the dry layer. In general, an SAP polymer provides 400 g/g absorption, and there are many SAP producers on the market.
The one used for battery cases is a high absorption version for water-glycol mixtures, and at 50% relative humidity in the air the absorber shows a mass change of 30-50%. If there is a lot of condensate, 200 g can be absorbed just from humidity, so the layer can swell from 2-3 mm to 10 mm. It is also tested to the UL94 flame-retardant standard.
The advantage of the SAP-based material is that decreasing the humidity immediately decreases the weight of the material, and with no hysteresis. This is a key difference from silica gel, which does have hysteresis.
This lack of hysteresis and the fast drying allows the material to be used for passive climate management, adapting to the humidity in case. The case is an open system with venting, and the change in humidity comes from air exchange in pressure differences, for example in a tunnel, going past a truck or with the temperature change between night and day.
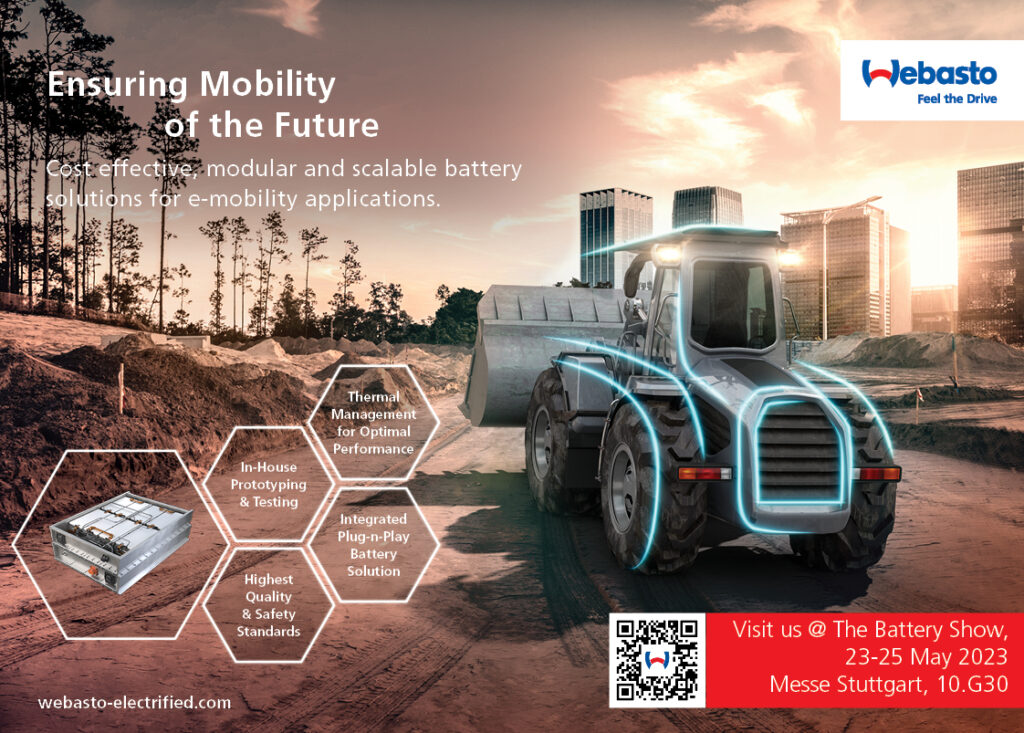
The question is how much free air is present in the case, and that leads to discussions with the designers about the conditions. These determine the amount of SAP used in the material and the positioning of the material.
That in turn leads to the design of the layer in the pad with the SAP, but there is a limit on the amount of SAP that can be added. That is because pure SAP slows down the absorbing process and re-drying, so the layered non-woven structure drives the performance.
Development work is continuing on increasing the amount of SAP that can be held in the non-woven layers, as well as reducing the weight of the fibres, which could be different types. There is also work on speeding up the absorption.
A key advantage with this approach is that it can be used as a design element and also as a running change to implement a retrofit. For a retrofit, it does not need additional space in the case. This is different from retrofitting a silica system to address condensation problems, as most of the silica approaches use a cartridge system or silica bag, which need fixing and can be heavy.
The important question is how much space is available for the swelling of the material, and that is also is part of the design decision. To manage a coolant leak the material would be on the bottom of the case. For condensation it would be on the bottom but next to the cold plate. To manage humidity the material can be placed on the bottom, side or top.
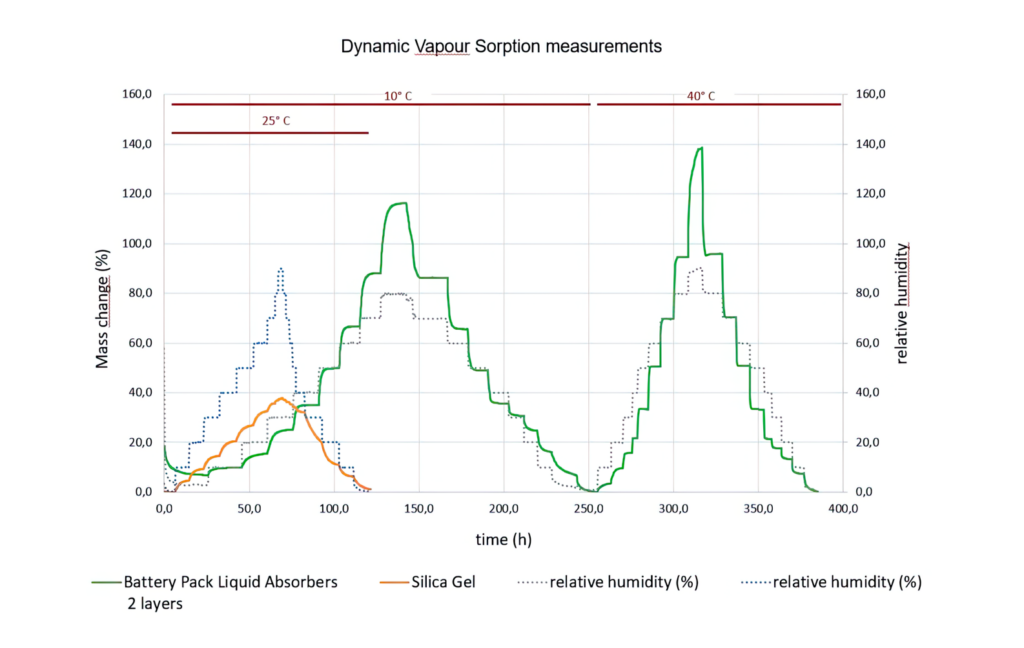
(Courtesy of Freudenberg)
Conclusion
The choice of materials used for a battery case has to cover a wide range of performance issues. Replacing steel or bonded aluminium with thermoplastics or glass fibre composites is offering lighter cases and more options for increasing the energy density by using larger components that can be more easily assembled. That opens up more modular design opportunities for recycling the cases
Other materials are also vital though. New flame-retardant additives for resins and coating materials for composites can boost a case’s thermal performance, but can require new application technologies such as spray heads.
Managing the moisture in the case for avoiding corrosion is also vital, whether from airborne humidity or leaks of the cooling system. New absorbent polymers in non-woven materials are providing more options for vehicle developers, for new platforms as well as retrofit.
Acknowledgements
The author would like to thank Lucas Krahl at Henkel, James at Ionetic, Christoph Ebel and Christian Schludi at SGL Carbon and Dr Ulrich Schneider and Patrick Richly at Freudenberg for their help with researching this article.
Some suppliers of battery case materials
Canada
China
ADV Cooler
EMP Tech
Trumony Aluminium
+86 135 8426 7707
+86 180 2619 3705
+86 1358 4862 808
Germany
Covestro
Evonik Industries
Freudenberg Performance Materials
Henkel
SGL Carbon
Thyssenkrupp Steel
+49 214 6009 2000
+49 201 17701
+49 6201 800
+49 9 211 7970
+49 611 60290
+49 203 52 24569
Saudi Arabia
UK
USA
ONLINE PARTNERS
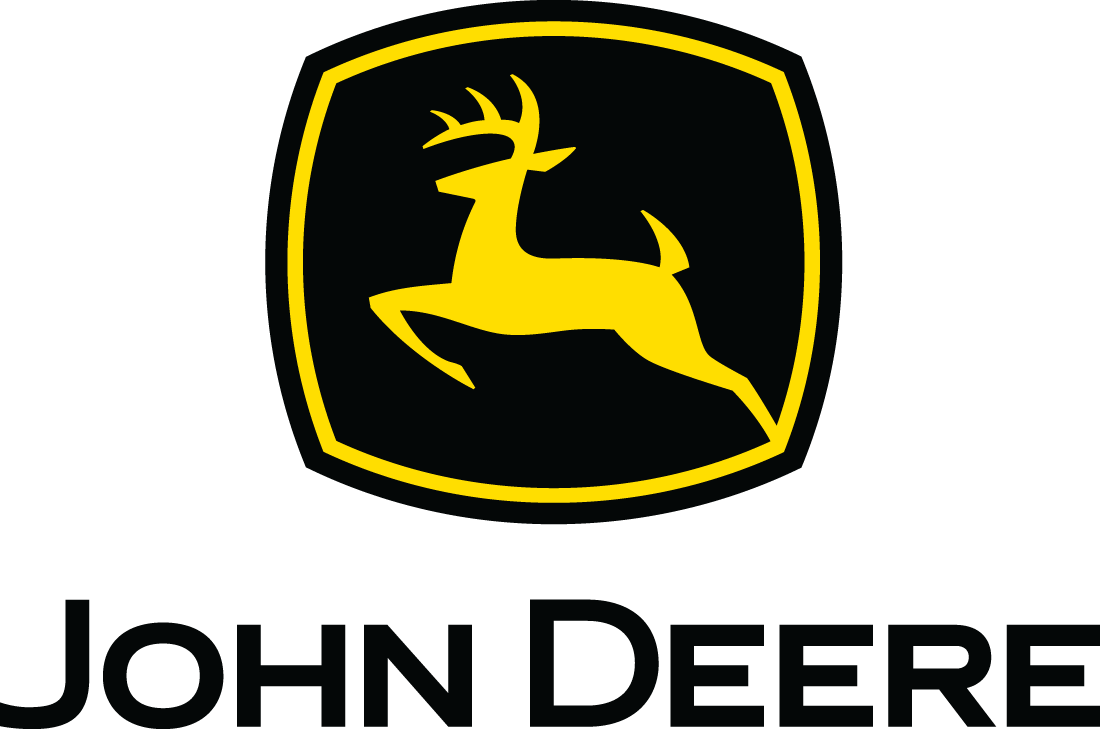
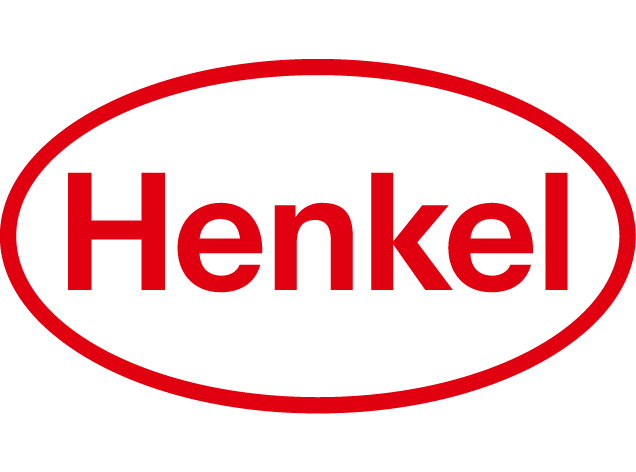
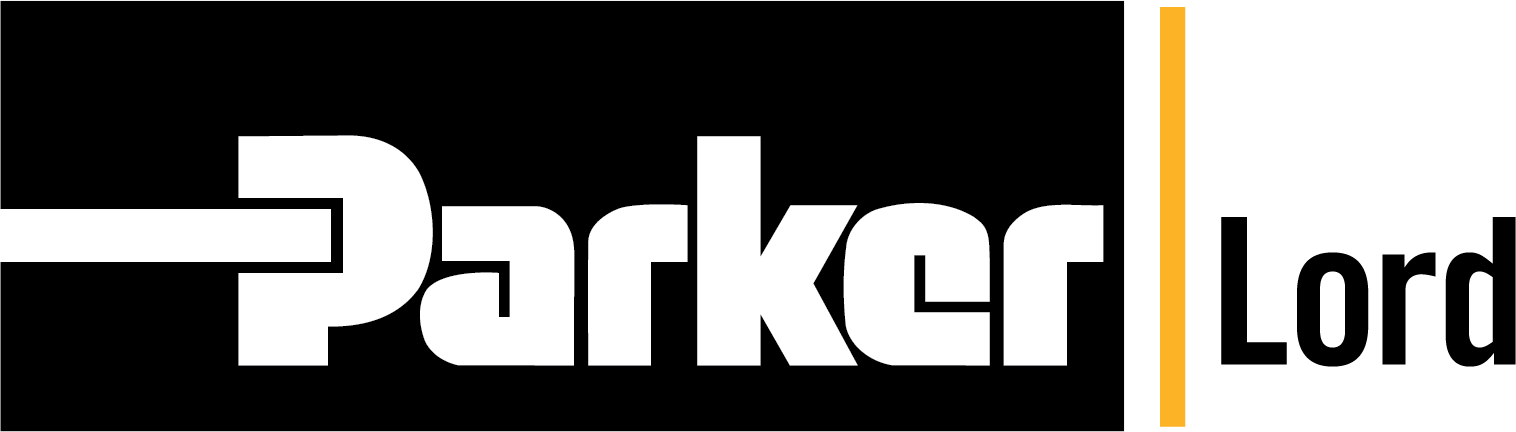
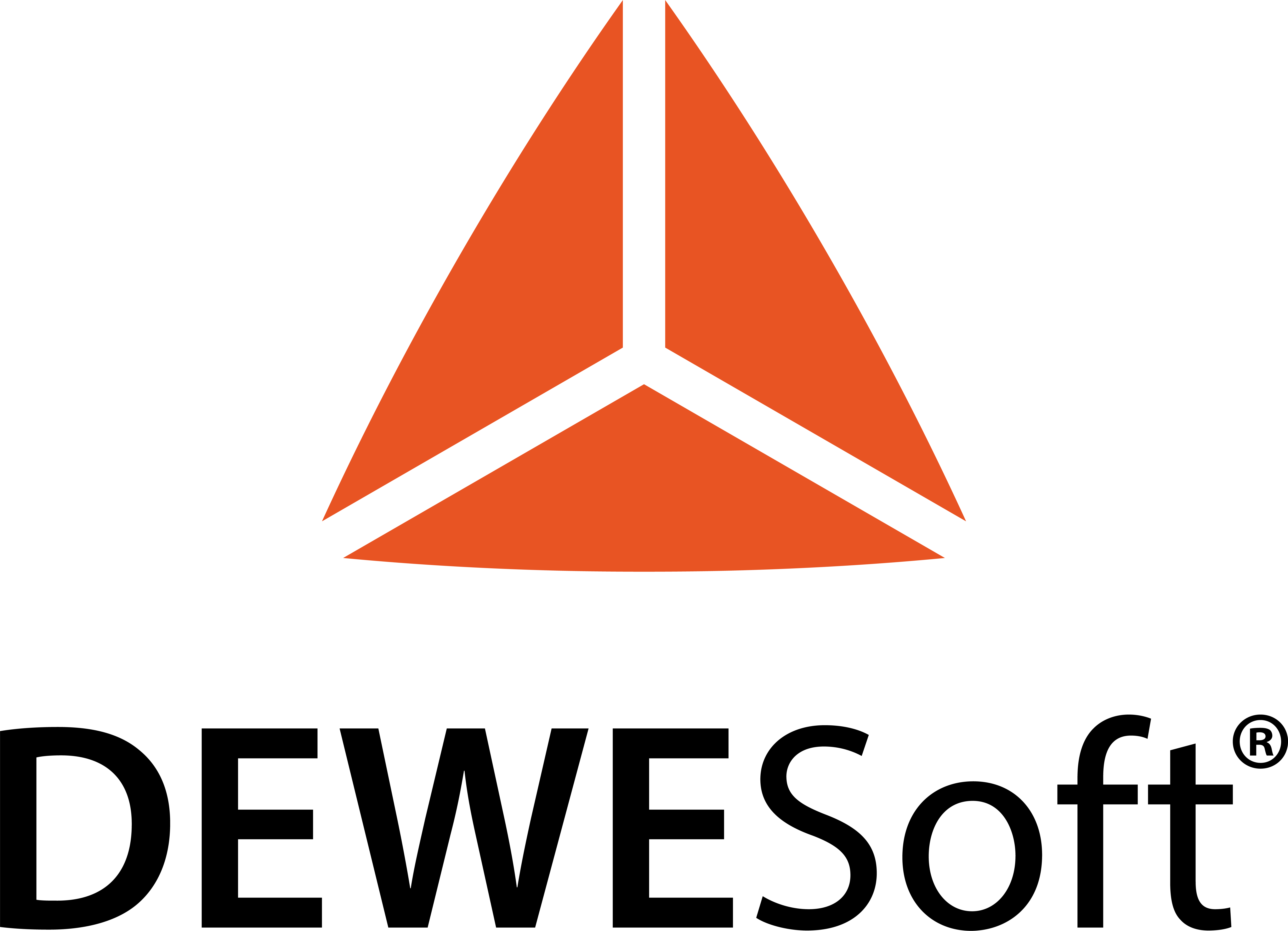
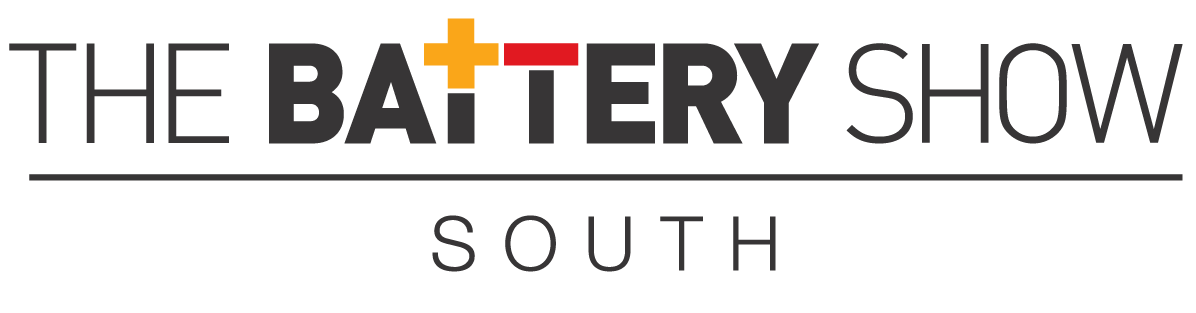
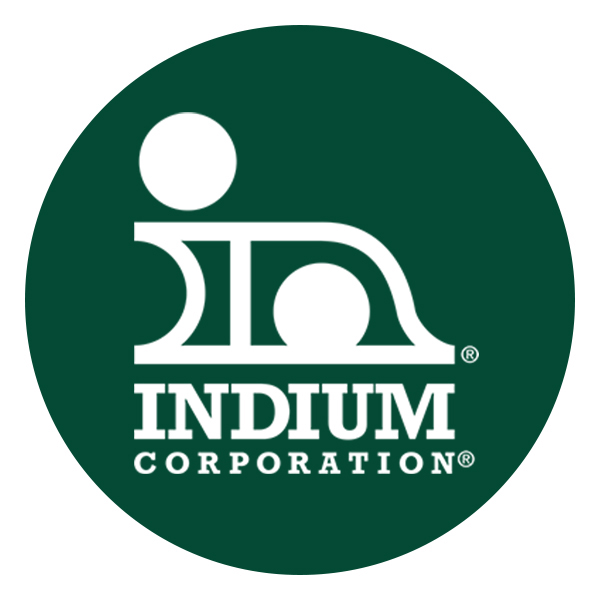

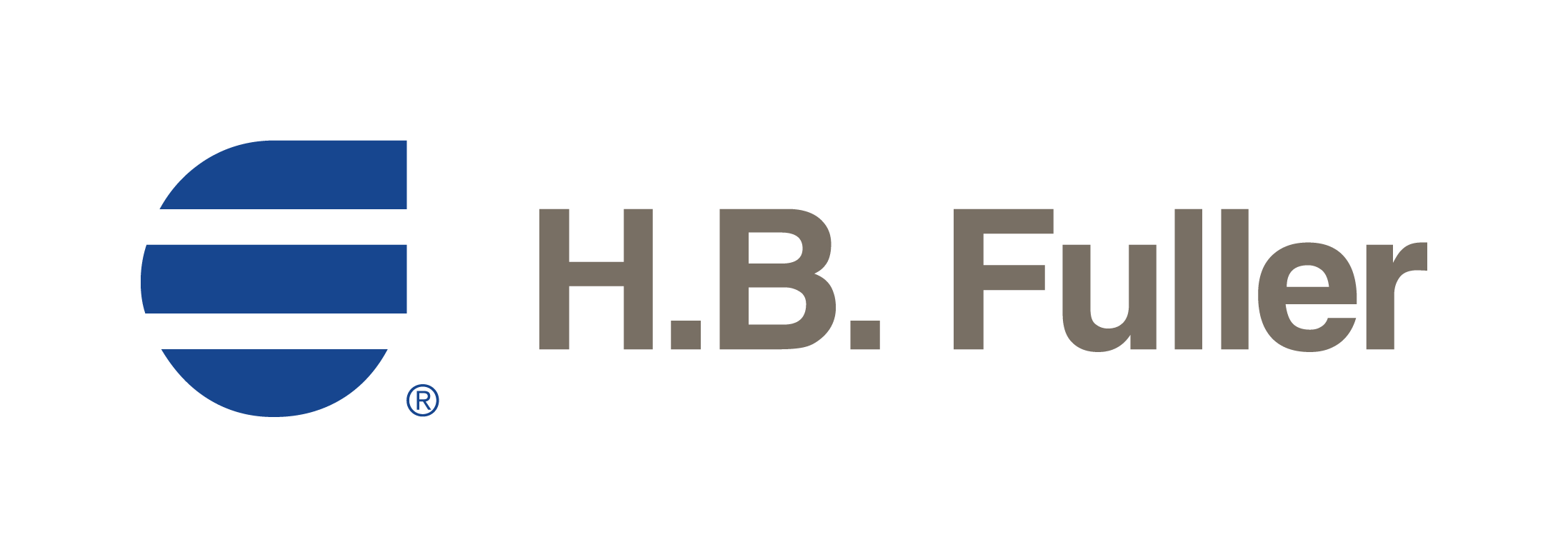
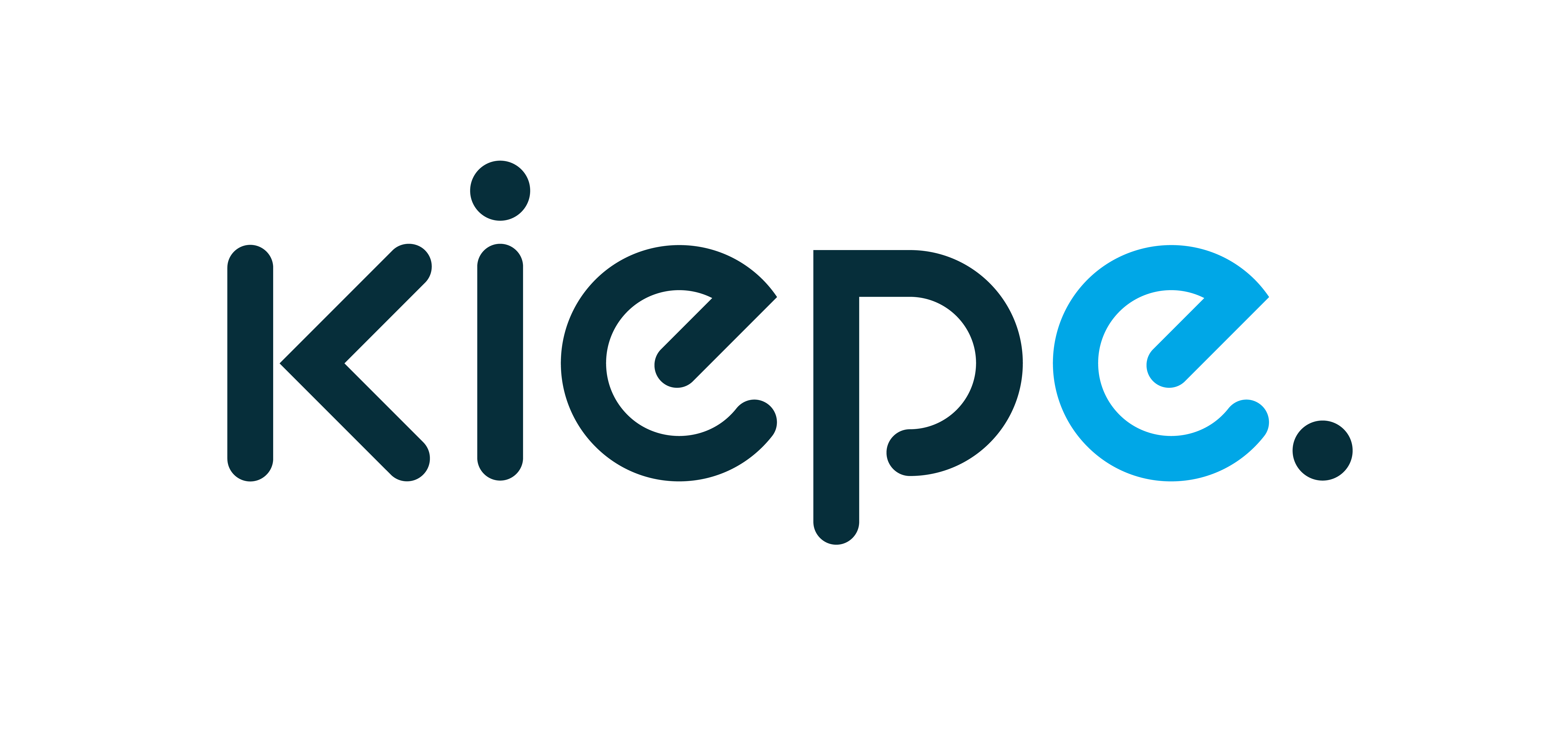
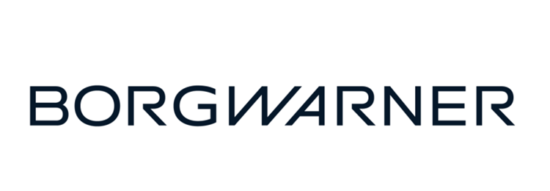