Eive electric 2CV
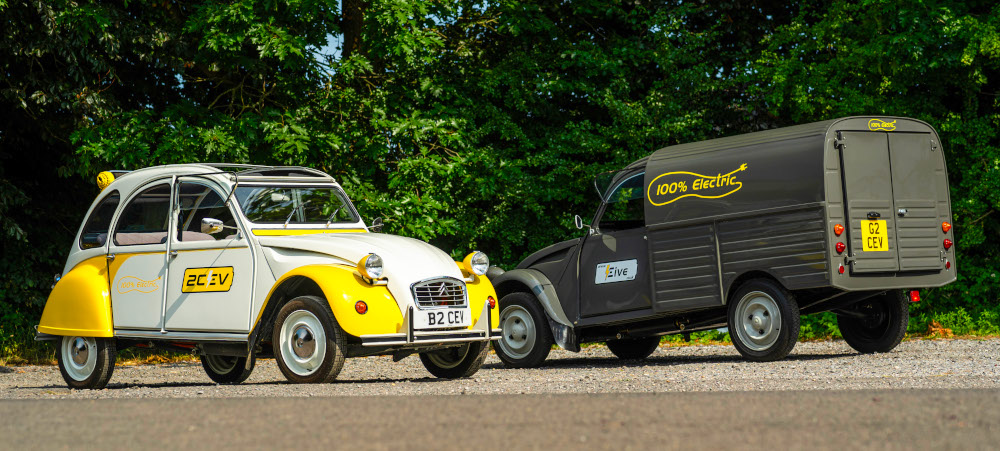
(Images courtesy of The 2CV Shop image)
French connection
This electric version of the classic Citroen van was developed in the UK using an e-drive from a company in France. Peter Donaldson reports
Electric conversions of classic cars such as original Minis and early Porsche 911s are now well-established, but the Citroen 2CV van created by The 2CV Shop in the UK is intended to carve out a niche of its own as a cute classic commercial EV it calls the Eive. Company principal Darren Arthur anticipates a market among small businesses that need to make local deliveries or visits and want a distinctive vehicle with a traditional image but with an eco-friendly twist – small bakeries, craft breweries, delicatessens and dog groomers, for example.
The Eive is powered by an electrification kit developed for 2CV spares manufacturer Mehari Club Cassis (MCC) by French company R-Fit. The body and chassis components are from MCC, and a custom-built van body is sourced in the UK, the whole vehicle being conceived, specified, marketed and constructed by The 2CV Shop.
New electric life
Although the prototype (which was displayed at the London EV Show in December) was converted to an electric van from a petrol 2CV saloon, Arthur emphasises that he intends production Eives to be offered as brand new vehicles. The company is currently working with the UK’s Driver and Vehicle Licencing Agency towards ensuring that they will be officially recognised as new vehicles.
All the body, chassis, and running gear and most of the powertrain components will be newly manufactured either by MCC, for which The 2CV Shop is the UK distributor, R-Fit, or Villevans in the UK, which supplies the GRP van body section.
The Eive has a stablemate in the form of the 2CEV saloon, with which it shares most of its components including the electric powertrain. MCC began renovating and customising the original Citroen Mehari, a lightweight utility and recreational vehicle based on 2CV mechanicals in the 1980s, and in 1998 Citroen transferred all the tooling for the Mehari to MCC, with the 2CV equipment following in 2000.
MCC started developing a new-build electrified Mehari called the Eden around 2016, selling the first of them 3 years later. Homologated in France and the EU, the R-Fit electrification kit is the basis of the powertrains of all three electric derivatives of the 2CV.
The 2CV Shop worked closely with MCC on the E2CV and the Eive, Arthur notes, to ensure that they drive as much like the original IC-engined cars as possible. “We didn’t want to just chuck a very powerful motor into a 2CV, make it go like the clappers and destroy the soul of the car,” he says. “We wanted it to be a 2CV but electric.”
Small battery, efficient motor
As integrated into the Eive van, the kit includes a 10 kWh lithium iron phosphate battery with an output voltage of 100 V. It provides the energy to drive a 20 kW synchronous, air-cooled DC motor with a peak torque output of 120 Nm and a quoted average efficiency close to 90%.
“We get a lot of range for the size of the battery,” Arthur says, adding that open-road testing with the van between the company’s premises in Wiltshire and the UK National Motor Museum in Hampshire, a distance of 47 miles, achieved a range of 68 miles from fully charged to flat.
“To get 68 miles from a 10 kWh battery is almost unknown. I didn’t hyper-mile it or drive really slowly, but the range test was not on the motorway going flat out, because that is not what the vehicle is designed for,” he says.
The Eive is set up with a modest amount of regenerative braking, Arthur notes. “It is not like in a modern car, it won’t stop you, but going down a steep hill during a test in southern France that was probably about a mile-and-a-half long it put about 2% back into the battery.”
In a test run around London with a 140 kg driver and a 198 kg load of 2CV gearboxes for part of the time, the mild regen contributed to a range of more than 75 miles during a day spent mostly in 20 and 30 mph zones, Arthur reports.
He attributes the ability to squeeze that kind of range from a 10 kWh battery to light weight and the low rolling resistance of the van’s skinny tyres. In future, he says, a larger battery will be offered as an option.
The powertrains of the Eive van and the 2CEV saloon are identical apart from the batteries; the van’s has the larger capacity and is consequently bigger and heavier. While the saloon seats four people, the van only has to seat two. That frees up space immediately behind the front seats for a larger battery and allows it to be positioned more centrally in the vehicle, which improves overall weight distribution.
Battery chemistry
Lithium iron phosphate chemistry, he adds, was chosen for its relative safety and tolerance. “What I like about LFP batteries is that you can fully charge them. I have a Tesla Model Three Long Range, which you are not supposed to charge fully unless you use it straight away. Our batteries are designed to be fully charged and left fully charged, although they don’t like being left empty.”
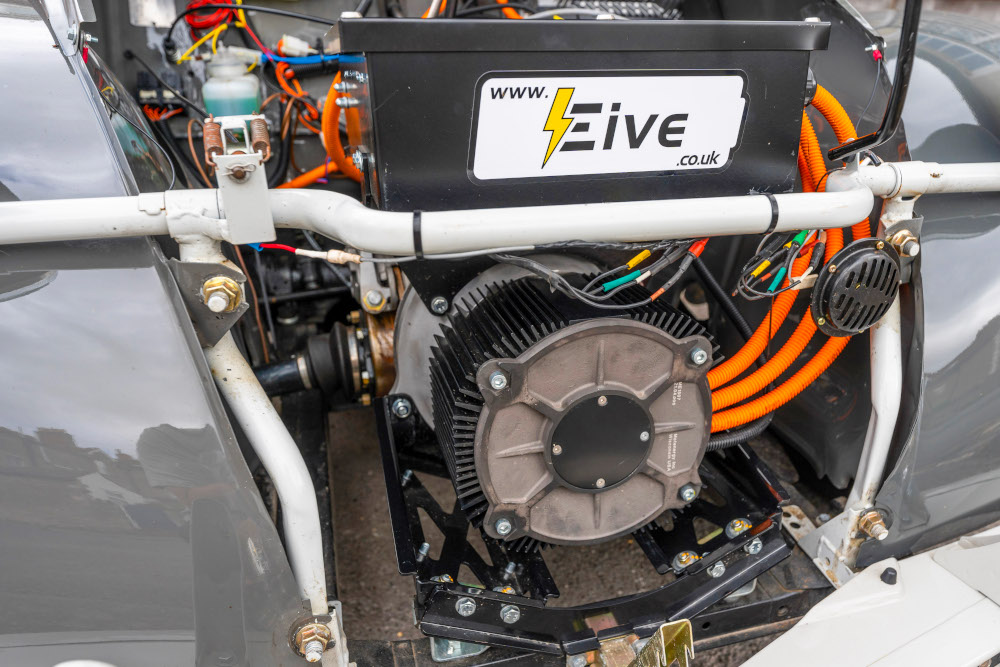
They will also retain their charge if they are unused for long periods, which he attributes to the fact that the electrified 2CV variants are not burdened with electronic systems that draw power when the vehicles are switched off. This is useful for Eden customers, many of whom keep them at their holiday homes in France, Spain and Italy. “They park them up for 6 months, and the car is designed so they can just turn up and drive it, and not have to deal with a flat battery,” Arthur says.
More important for the van is the ability to hold on to that capacity over a large number of charge cycles and many years. The Eive’s batteries are guaranteed to retain at least 80% of their original capacity after 2,00 charge cycles. “That means if you fully charge your Eive twice a week every week, it will take 24 years to reach the 2,00 charge cycles or about 175,000 miles,” Arthur says.
At just 10 kWh, the battery capacity is modest, but it results from the need to balance range with weight and cost. The van is a last-mile delivery city vehicle, he explains, and the battery was chosen accordingly. The pack selected weighs about 85 kg.
“We didn’t want to put in a huge amount of battery capacity in. In some classic car conversions I’ve seen, the car weighs a lot more than it did before, and that completely changes its character. When you drive the electric 2CV, it drives like a 2CV and, while it is ‘a few bags of shopping’ heavier the weight distribution is more 50-50.”
That has enabled Arthur and his team to retain the standard 2CV suspension on the E2CV, although the van’s rear suspension is uprated to cope with the greater weights carried in the back.
Because batteries are a major cost item in any EV, modest battery capacity helps keep the Eive’s price down. The corollary of that, he notes, is that even a substantial drop in the price per kWh of battery capacity would not make much difference to the van’s price.
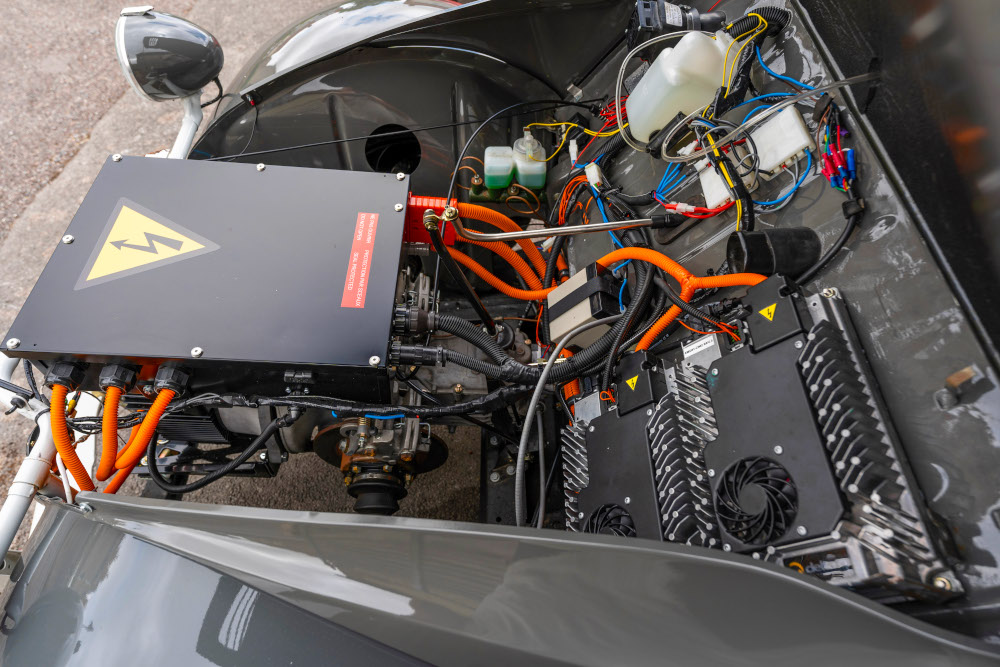
Keep it simple
In line with the keep-it-simple philosophy of the Eive’s development, the battery pack has no dedicated cooling system. None is needed, because the battery is relatively small and is charged and discharged at modest rates.
“You can’t really rapid-charge a 10 kWh battery, but if you could you would need liquid cooling for that,” Arthur says. “It has a 3 kW charger, so it’s just not stressed. Even if you go around with your foot flat down all day it is not going to suck the battery dry in a short time.”
Nor is the battery pack heated. “So far, our testing says we don’t need to do that,” he says. “Obviously, batteries don’t like cold weather, but we’re still not drawing on ours heavily.”
The prototype is fitted with two 1.5 kW DC chargers to obtain the 3 kW capacity. They were available when the team carried out the conversion, but production vehicles will have a single off-the-shelf 3 kW unit.
The charging system comes with a three-pin domestic plug for UK customers, enabling it to charge from any wall outlet, plus a Type 2 adapter. With a 3 kW charge rate, Arthur explains, the battery will go from 10 to 80% in two-and-a-half hours. “Basically, when you’re not using it, just plug it in.”
Lightness and simplicity were also the drivers behind the choice of the motor in the R-Fit kit. In the prototype it is a Motenergy ME1507, an interior permanent magnet synchronous (PMSM) motor.
PMSMs are very similar to brushless direct current (BLDC) motors, having the same basic architecture with permanent magnets on the rotor and windings on the stator. Both require the drive currents to be synchronised, with rotor position feedback typically provided by Hall effect sensors.
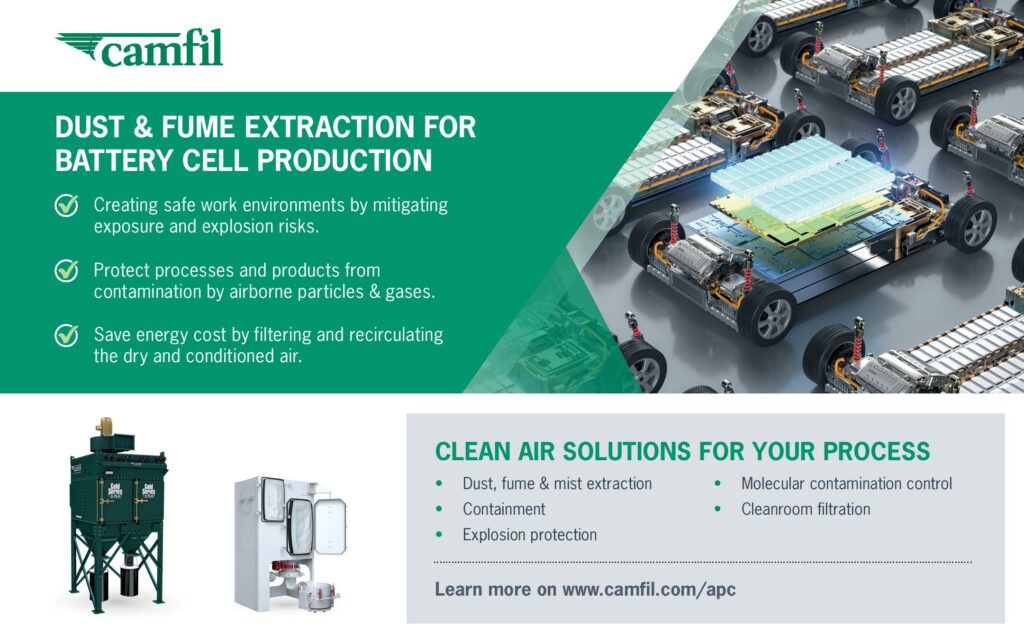
PMSM power, original transmission
Like BLDC motors, PMSMs work with DC input power, so the Eive does not need an inverter. The principal difference between them is in the drive signals, with the PMSM requiring a sinusoidal signal and the BLDC a trapezoidal one.
The sinusoidal drive signal makes PMSMs quieter and almost eliminates torque ripple. Each type is driven by a PWM three-phase bridge to supply the motor with variable voltage and current frequencies and amplitudes.
The motor’s torque has to be limited to protect the standard 2CV transmission, and the controller is programmed with a tailored torque curve rather than a crude limiter, allowing it essentially to replicate the performance of the original IC-engined van.
MCC makes a special bellhousing as part of the electrification that mates to the motor to the four-speed transmission and retains the clutch.
Most of the time, the vehicle would be run in third gear, but second and fourth are also available to boost torque to the wheels and extend the range respectively. The clutch is used when changing gear on the move, but is not needed to move off from a standstill. Reverse gear is also used, as it would be in the IC-engined vehicle, but first is blocked off. “It just spins the wheels and doesn’t do anything,” Arthur says. “Also, it could spin the gearbox up too fast and damage it.”
One option that MCC offers for the Eden, known as Eden Easy, locks the gearbox in third to go forwards and changes the polarity of the motor to allow it to go backwards in first.
On opening the van’s bonnet, the view is dominated by the control module, a large black box containing electronic and electrical components such as the BMS, contactors and the pedal position sensor, the latter being a potentiometer connected to the 2CV’s standard accelerator pedal and steel cable set-up.
The control module sits immediately above the motor and stretches back past the bellhousing and over the transmission as far as the differential and driveshafts. As with the original, all the machinery is clearly visible, with plenty of space around it.
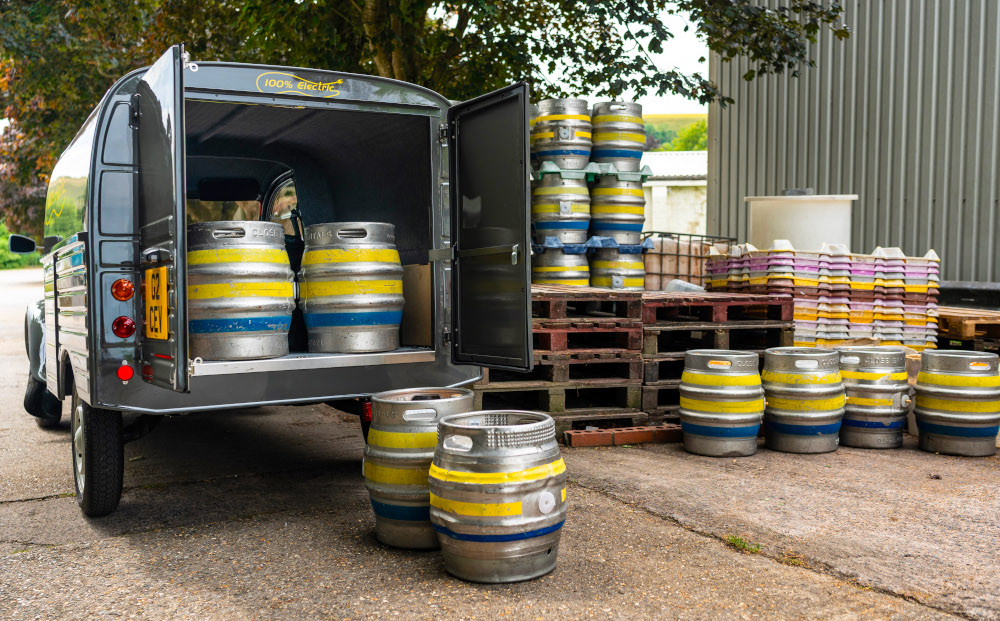
Structure and bodywork
The Eive is based on a standard 2CV saloon chassis, suspension and bodywork, and no major modifications have had to be made to integrate any of the electric powertrain, Arthur says. The 2CV has a separate chassis and body shell.
“As we use the floor pan of a 2CV saloon body shell, not that of a van, there’s room behind the seats to put the battery,” he says. “It wasn’t designed for it because the van kit was designed a long time ago, but it is perfect for a battery. There are no major modifications, just a few holes for cables and so on.”
In the 2CEV saloon, the battery is in the boot behind the rear passenger seat. With the kit that comes from MCC, the battery is designed to go into the boot with no modifications to the bodywork. However, The 2CV Shop has designed its own mounting kit that allows the battery to sit lower but which requires two mounting holes to be drilled in the body shell floor for a support bar.
While the front suspension is standard 2CV saloon equipment, the suspension has to be modified at the rear because the van was designed for heavier loads. The core of the modification involves cutting open the tubes that contain the rear springs and replacing the standard coils with uprated units
The Eive’s most obvious difference from the saloon is the van body, which gave Arthur a choice. “We could take an original 2CV van, in metal, and convert it to electric power, but good 2CVs are hard enough to find, and vans are extremely scarce,” he explains. “Because they are at least 45 years old and there is a lot of metal in the panelwork at the back and the tin worm [rust] has got into it, it is a lot of work to make an original van.
“If I were building two a year I would convert originals, but I don’t know how big the market is for the electric van,” he adds. “It’ won’t be massive, but let’s say I sell 10 a year, I couldn’t find 10 2CV vans in a year, every year, and those I could find would be worse and worse.”
He adds that the original van, known as the Fourgonnette, also had some practical limitations as a commercial vehicle from an internal space point of view. Its inner wings take up a lot of room, and house the fuel tank on one side and the spare wheel on the other. The fibreglass body from Villevans, however, offers a wider and more open space inside.
“Yes, an enthusiast will know the difference, but most people will just see a cute van,” Arthur says.
Chassis manufacture
MCC’s steel 2CV chassis is galvanised for corrosion protection, while the frame that The 2CV Shop makes to hold the body on to the chassis is fabricated from stainless steel. The rest of the bodywork is made from steel with an e-coating to keep the rust at bay.
Appropriately for an EV, the 2CV’s chassis has always been very skateboard-like. Construction at MCC’s facility begins on a jig, with the first stage consisting of assembly of the two inner longerons slotted onto air pair of large diameter transverse tubes front and rear.
Smaller structural parts are then fitted between the longerons, including the support for the front seats and the front and rear reinforcing arches, which lie horizontally and a rear cross-member. These components are then clamped in place and spot-welded together, then moved to the next assembly stage on second jig.
Lying on this jig is the steel sheet that will form the chassis’ bottom plate. Further spot-welds are made and reinforcing channels are slotted into the open sections of the longerons. The top plate is then put in place and fixed with numerous spot welds with the aid of a template to ensure they are positioned correctly.
The chassis is then moved to a third fixture and fitted with its outer longerons, which are also spot-welded in place with the aid of a template. A fourth stage involves putting the chassis into a machine that folds over the edges of the longerons. In a fifth stage, the chassis is placed in a machine that drills all the holes for the external accessories.
The accessories, including suspension supports and towing loops, are welded on in the sixth stage, after which the chassis is placed in a roll frame that allows access for attachment of the rest of the mounts for the front and rear running gear and the fuel tank support member in the final stage.
Essentially complete, the chassis is then treated to prevent corrosion, being either hot-dip galvanised or put through a cataphoresis process that electrochemically deposits an epoxy-type coating.
The separate body shell structure is then assembled and spot-welded on a jig from pressed steel panels.
Integrating the van body
Using a standard 2CV saloon shell, even a brand new one, as the starting point for the van involves significant surgery, Arthur explains. Starting just behind the B-posts, immediately to the rear of the doors, the shell is cut down to the level of the floor and the sills, which are retained, so the roof and all the vertical panels behind what will become the cab come off.
A steel framework is then welded to the B-posts, the cab roof and the floor and sills to provide a structure to which the van body can be joined. A reinforcing frame is then also welded to the floor and sills. Finally, the fibreglass van body and its stainless steel supporting frame are bonded and bolted to the new structure.
“Eventually, we will be getting the bodyshells made so that we don’t have to cut the back end off the car, once I know what numbers we are selling,” Arthur says. “If we’re only doing one or two a year I won’t bother, but if it’s 10-plus then I’ll get the bodyshells made so we just bolt the fibreglass body on.”
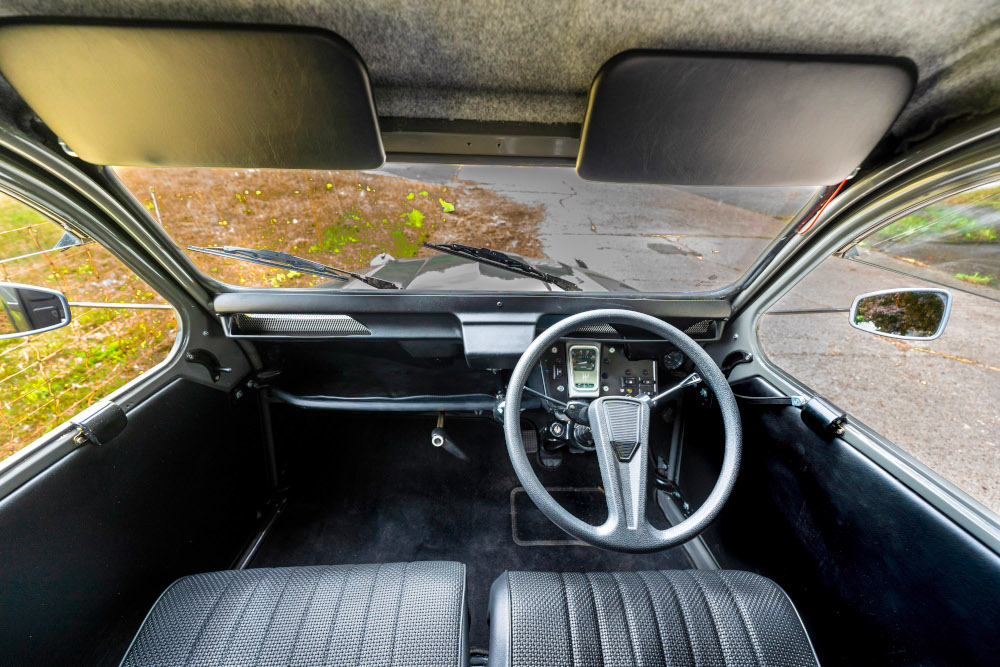
Basic interior
The interior is deliberately kept as basic as the original, with only the addition of an analogue battery gauge, a second heater/demister to meet UK regulations. A USB port is an option, and heated seats are likely to be offered in the future. “Heated seats don’t take much power, and they do a good job,” Arthur says.
Priced at £40,000 plus VAT in the UK, the Eive will not be cheap, Arthur admits, but it will be a niche vehicle that will stand out and act as an ambassador for a small business, he says, and leasing packages are available.
If all goes to plan, the first vans will be delivered to customers this August, a couple of months after the first 2CEV saloons take to the road.
ONLINE PARTNERS
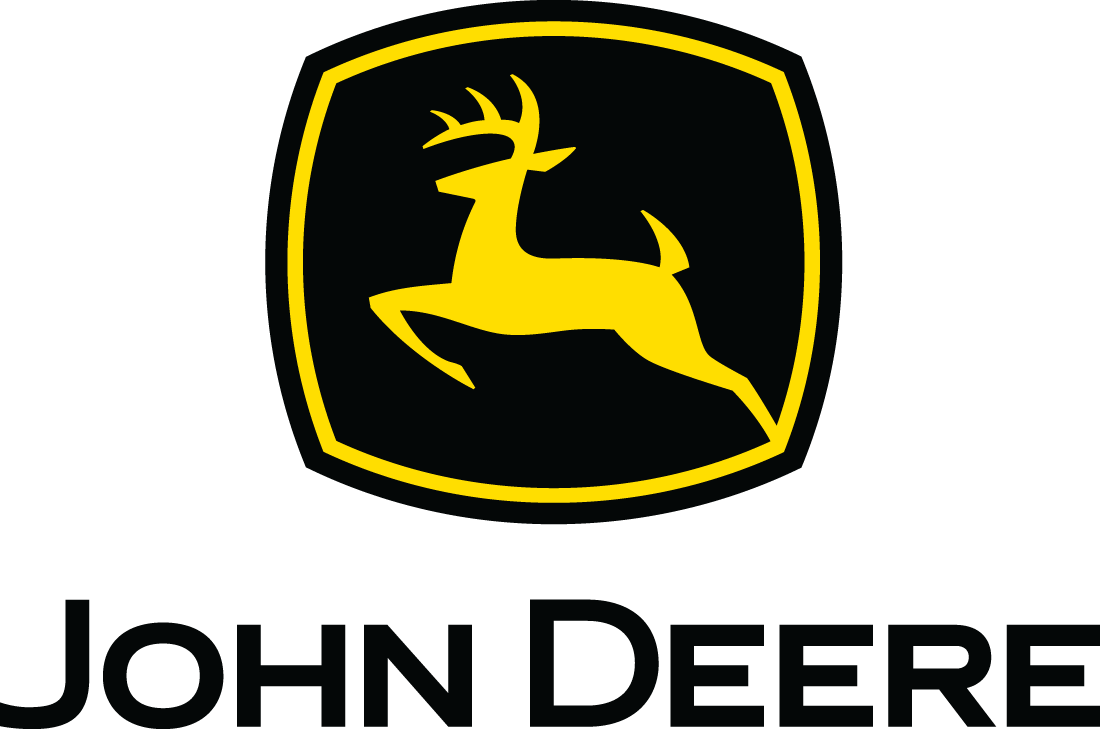
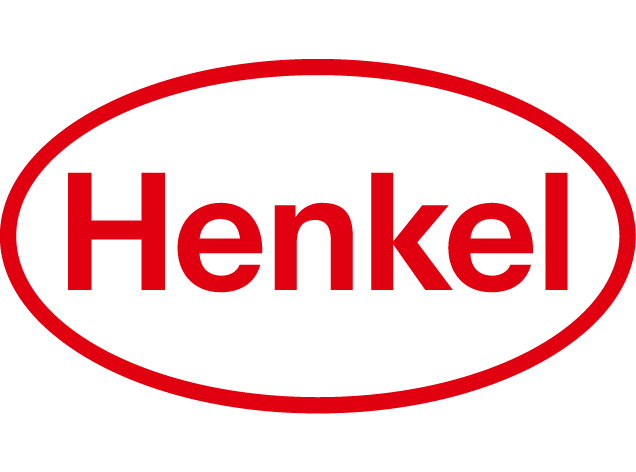
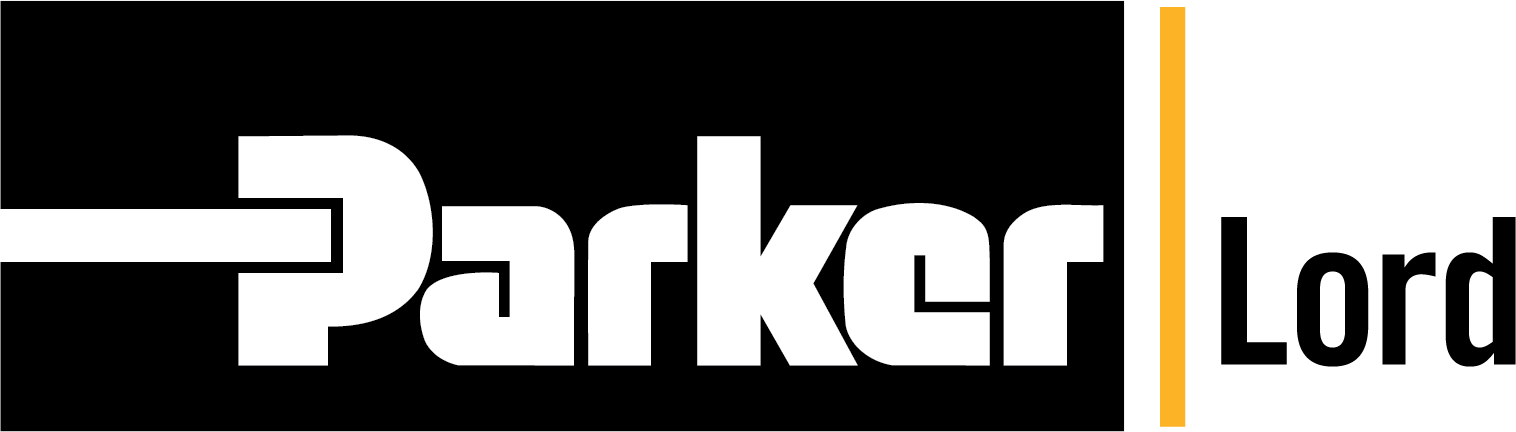
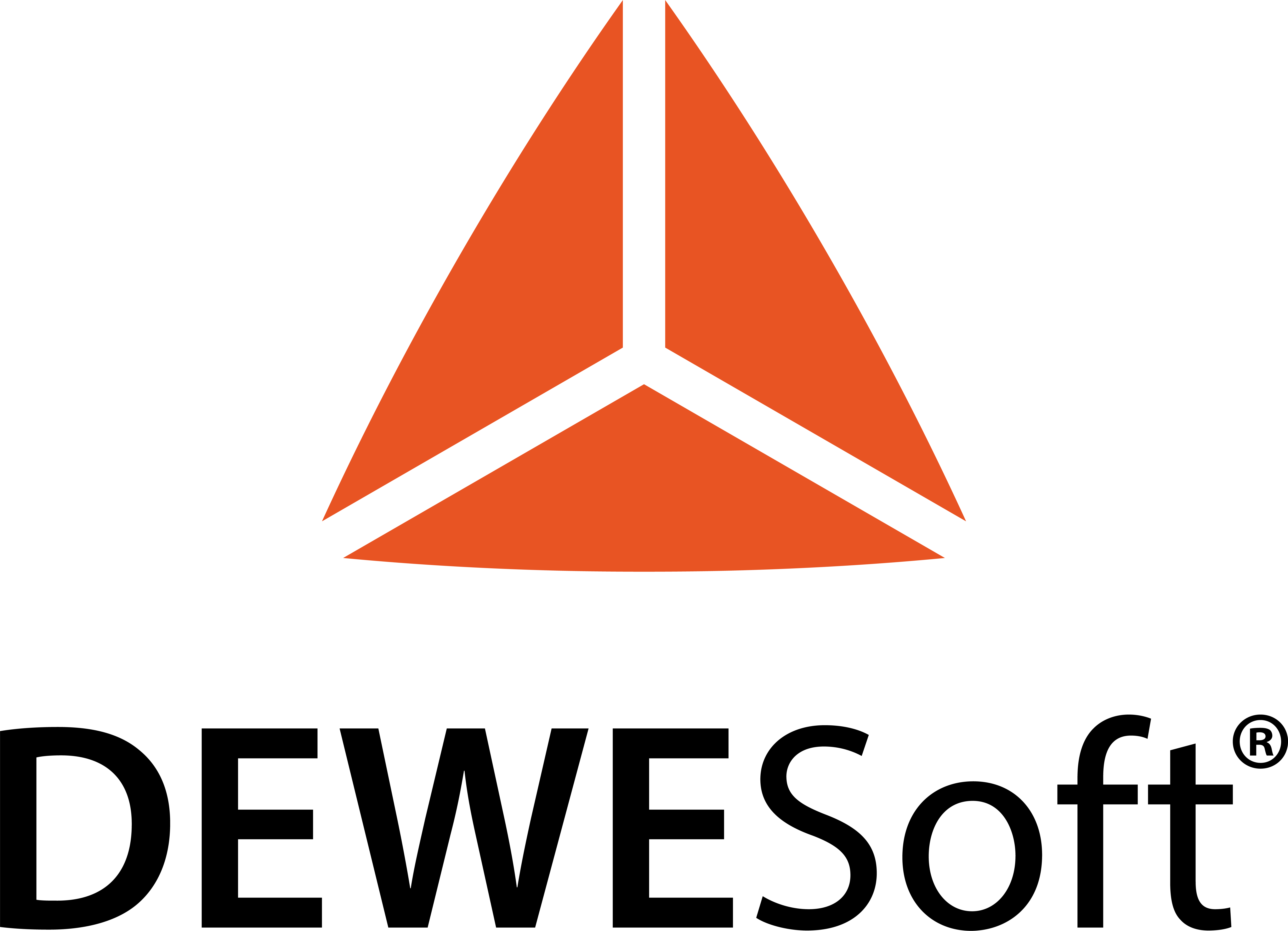
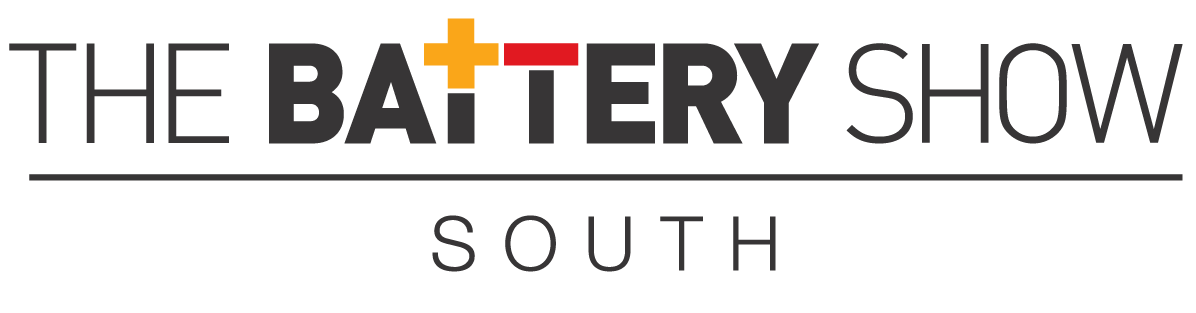
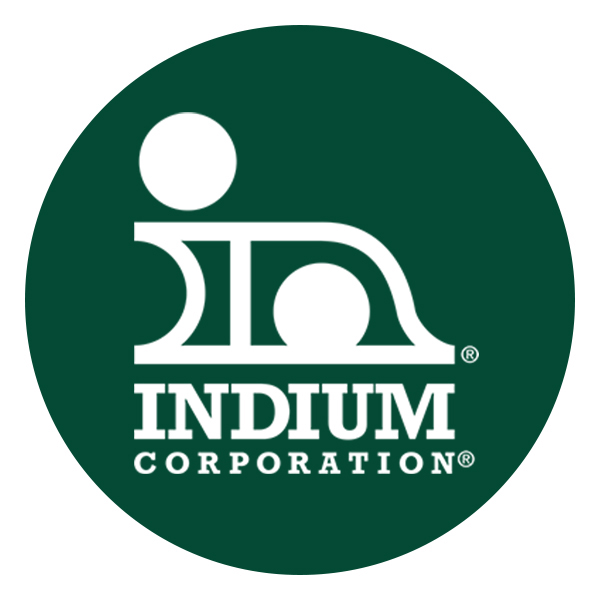

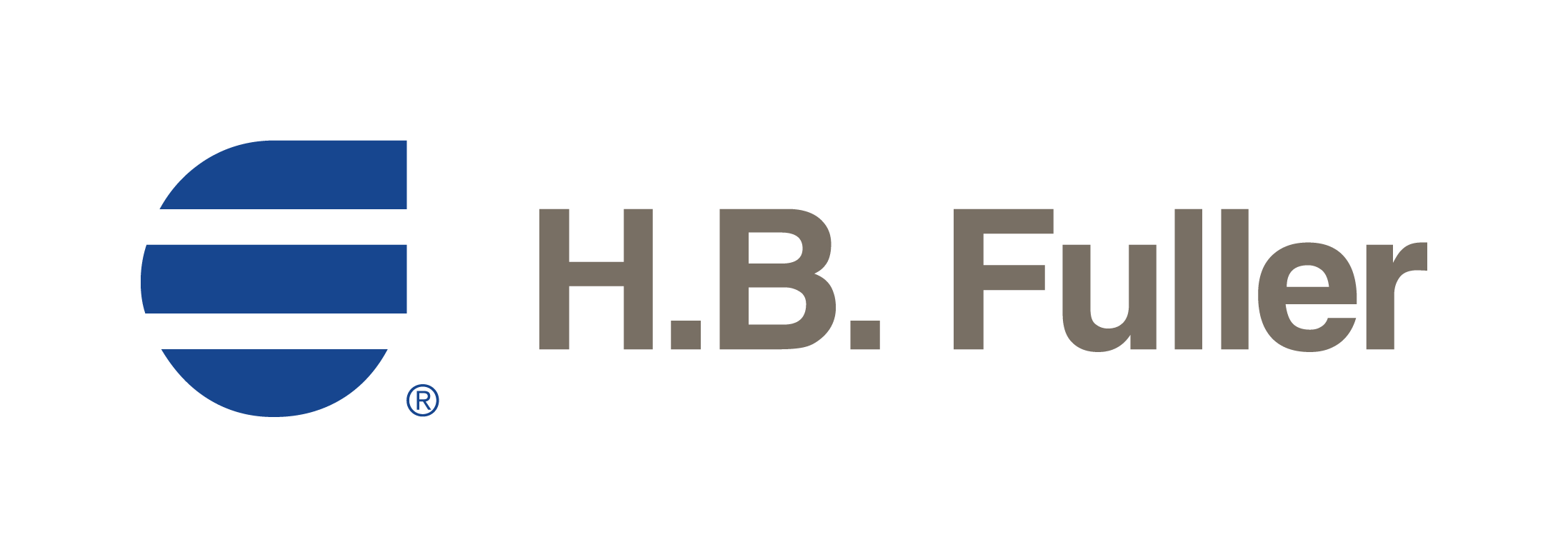
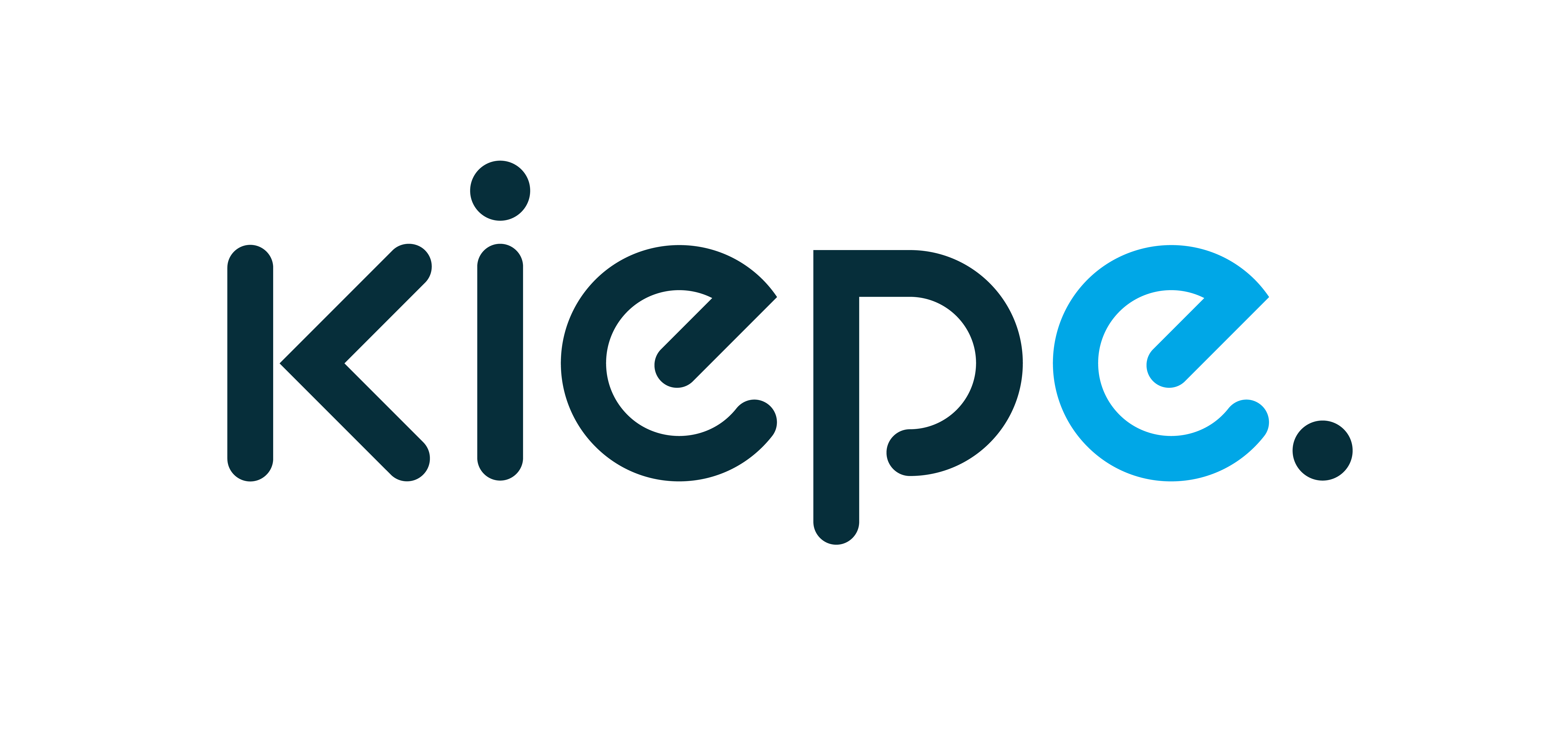
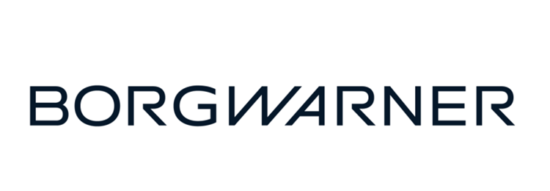