Asher Bennett
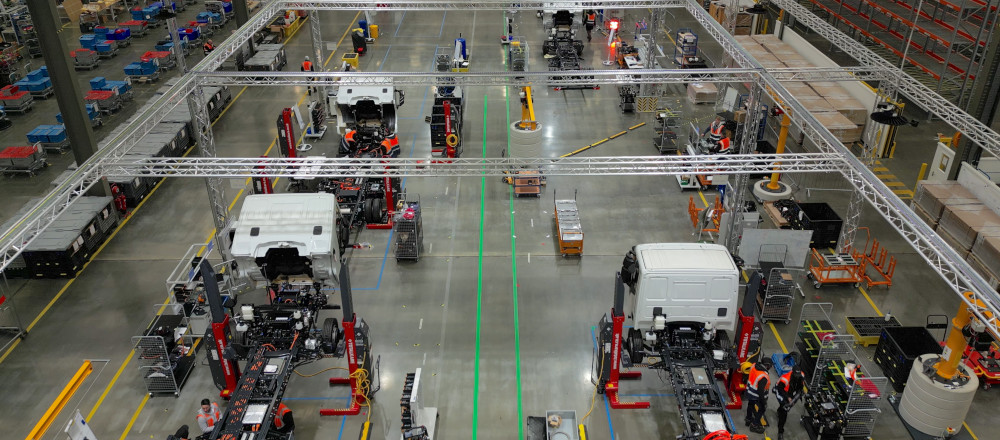
(Images courtesy of Tevva)
Hybrid haulage
The CEO of Tevva Trucks explains his thinking behind offering goods vehicles with a dual energy system. By Rory Jackson
One of the most prominent differences between Tevva Motors, based in Essex, England, and other EV manufacturers is that its 7.5 tonne battery-electric and hydrogen-electric trucks originated not from motorsport or automotive OEM innovations, but from the world of submarines.
Tevva’s CEO Asher Bennett says this story stems from his days in the Israeli Navy, on a submarine that also happened to be his first electrified vehicle. “It was a Gal-class, British-built submarine, and the entire bottom of the vessel was a big bank of batteries, with a large electric motor connected to the propshaft and propeller,” he says.
“That meant we had to understand electric powertrain systems. But of course, back in the 1990s, an all-battery vessel would have soon needed to return to its base to recharge. So it had a dual energy system, the non-battery half being a back-up diesel generator, which ran on fuel stored onboard and air collected using a snorkel.
“We would pre-plan our energy usage levels days and weeks ahead, to make sure the batteries’ SoC wouldn’t run low at tactically inopportune moments, leaving room for adjustments where needed,” he says. That concept of a dual energy system with pre-planned energy management is at the heart of the trucks and why they are available in fully electric as well as hydrogen-augmented versions.
Bennett worked across a number of IT firms after his naval service, including e-commerce and cybersecurity, but returned to electric powertrains in 2008 after co-founding and becoming CEO of a company called Evida Power. Evida was set up to provide lithium-ion pack designs and technologies, as well as EV integration services, to commercial fleets for customers around the world.
“That was 14 years ago, during the pioneering days of commercial EV technologies, and we had projects with a lot of EV start-ups, including the Beijing Olympics electric bus project. A fair amount of that work was with what was then a very small outfit called Tesla,” he says.
While building up experience of prototyping, cycling, crash-testing and homologating batteries, Bennett was keeping an eye on the growing world of EVs and became curious as to why so many were working on electric cars while comparatively few were developing electric buses, and fewer still were bothering with electric trucks.
“Although the physics of moving a 15 t bus or truck are roughly the same, they’re operated in very different ways, as well as being financed differently, so you need very different solutions for both,” he says.
“We realised that trucks not only need a very cost-effective powertrain solution, but in most cases they just won’t stop during the day to charge. Some people think truck drivers take a break every few hours, maybe taking 30-60 minutes to find a charging station for a top-up, but that’s never going to happen in the world of trucks.
“Certainly, they save money on every mile driven electrically compared with diesel, but they need to drive a lot of those miles to justify the initial capital expenditure, and without stopping to charge.
“Fleet managers will only send them out in the morning if they’re guaranteed to complete their day; these days, a truck driver’s day can take many different forms and sets of objectives, but in the medium-weight classes we’re initially targeting, it means they have to come back to their base after successfully completing all their routes over 8-10 hours of driving.”
Although Bennett and his colleagues are witnessing the first of their trucks being driven by prospective customers in commercial trials, he notes that, given these various caveats, getting there was by no means easy or straightforward.
Company background
Before founding Tevva in late 2014, Bennett and his colleagues spent 18 months planning the business and assembling their team, before taking several months to build their first prototype.
“That still sits on our facility’s grounds, and provided us with huge amounts of data from tests and adjustments after making it road-legal and a prototype project with UPS,” he recalls.
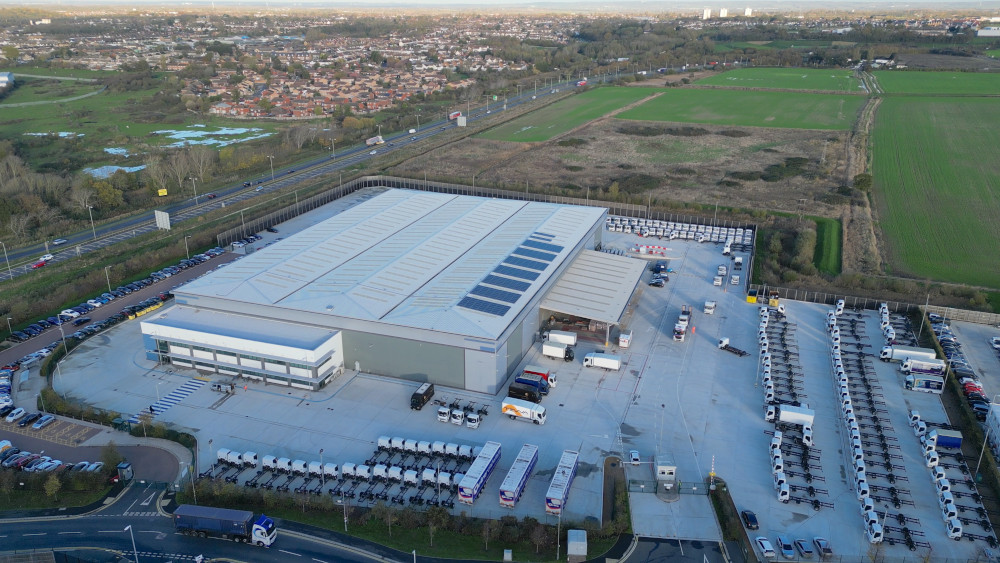
“The UPS project involved us building a road-legal truck for them, which they road-tested for the following 15 months. That in turn gave us even more test data and a small order from them later on.”
The UPS order motivated Tevva to develop a low-volume production capability, and it began delivering truck to UPS in late 2019, which are currently operated by the courier in various parts of the UK. “There were other small projects along the way, but those – including making it through Covid-19 and furlough – led us to where we are now, a company of 300 people,” Bennett says.
Alongside the data coming from its customers, in-house r&d has included closed-track tests and road trials running from Lapland to Spain, to optimise the trucks’ robustness.
In addition, a range of cycling, crashing, burning and puncturing tests have enabled Tevva to optimise its batteries for safety, with cell choice having played a considerable part in this, and to give trucks a commercially viable range, power and so on.
This has culminated in several dozen Tevva prototypes operating on public roads, all of which have passed verification tests for braking, steering and other safety-critical systems.
Battery chemistry
Although Evida specialised in battery engineering at the module and pack levels, Bennett and his engineers have kept a close eye on the range of cell chemistries and form factors to select the right cells for their application.
“We chose a large-format, prismatic, lithium iron phosphate [LFP] system as our cell,” he says, “LFP is now a mainstream tried-and-tested chemistry, which makes it reliable and freely available.
“We know effectively how cell development works. A new cell technology is developed, then you make some adjustments: maybe you use a thinner cathode foil, a thicker separator, a different electrolyte recipe and other minor things.
“If you want to test it, you can cycle it 2000 times, effectively replicating 2 years’ worth of 8-hour driving days. But it’s a lot of work, and there is a cost and risk involved in maturing a totally new cathode material.
“We avoid the need for such experimentation and testing, as LFP has the longest life cycle of any mainstream chemistry. It’s considered the safest, and it has a wider thermal envelope, meaning we don’t have to heat or cool it as much as other chemistries. That reduces the size and weight of the thermal management systems onboard our trucks.”
All cells have their downside, Bennett notes, and he concedes that LFP cells have a slightly lower energy-to-weight ratio than other mainstream chemistries. However, he views that as a worthwhile trade-off for a truck, which needs optimum lifespan and safety rather than saving weight.
In the meantime, Tevva has the freedom to adapt new cells as costs and benefits change, although the process of adapting entirely new cells into its modules takes a few months of r&d.
“That’s a quick turnaround relative to elsewhere in the industry. We’ve long known how to engineer everything above the cell level, from the local BMS components at the module level to the global BMSs, safety systems and cooling systems at the pack level, and management of network comms going out to the vehicle’s other subsystems,” Bennett adds.
“As well as doing obvious things like calculating SoC, SoH and so on, that enables behaviours suited to the trucks’ operational profiles, for example having the BMS tell the truck to slow down when the battery’s hot, or maybe identify a GPS coordinate and route towards a safe place to stop and cool down within the upcoming map area.”
Hydrogen power
Tevva’s expansion into hydrogen-electric powertrains has come alongside its r&d into larger vehicle weight classes, as well as the recent granting of European Community Whole Vehicle Type Approval for supplying its trucks to European markets (with both left and right-hand-drive versions already being assembled at its factory).
Bennett however views hydrogen as only part of the dual energy system. “Hydrogen gives us electrons, which turn the motor just as electrons from the battery do, or they recharge the battery, or both, depending on how we operate,” he says.
He notes here that electric cars are now mainstream. In the first half of 2022, 16% of new passenger cars in the UK were electric; in Germany for example it was 24%. He puts that down to the average passenger car being driven for 1 or 2 hours a day, with most outliers beyond this usage being covered by the cars’ total ranges between charges.
“Truck and fleet managers have far more stringent requirements though,” he says. “Moreover, there’s no such thing as an absolute given truck range for a given specific energy: the range you achieve will vary according to road conditions, payload, weather, the use of air conditioning and so on.
“Those changes are sharp enough in passenger cars, but the sheer mass of trucks means that variance gets even higher, with up to 30% swings in empirical ranges just from changing between a good truck driver and a bad one. And other truck-specific burdens such as power-demanding refrigeration trailers can be even worse.
“Fleet managers never worry about getting the job done when they’re using diesel trucks. Refuelling isn’t always needed, but if it is, it takes 10 minutes. Battery-electric ones don’t have that freedom, and fleet managers don’t have time to start calculating expected ranges for all the variables and more beyond what I’ve listed.”
Bennett therefore sees the battery-electric versions of the trucks – with their 105 kWh packs, 227 km maximum ranges, and 2952 kg payload limits – being used for short, repetitive routes in flat regions, to realise the economic benefits of driving on electric power without needing to recharge outside overnight depot stays.
“We could double or triple the battery energy to get more range, but that would add prohibitive amounts of weight, and as it stands 105 kWh covers 80-90% of short-haul needs,” he says. “Hydrogen meanwhile has much better specific energy than lithium-ion, with a 100 kg hydrogen cylinder giving us at least the energy of a 600-700 kg battery once it’s run through our fuel cell.
“It’s also fast to refuel, typically around 10 minutes, making it competitive with diesel in fleet managers’ turnaround expectations, as well as being clean. But we haven’t gone all-hydrogen because hydrogen will remain far more expensive than grid electricity and diesel for at least the next few years.
“Fuel cells will also remain rather expensive for the time being. If we went fully hydrogen-electric, we’d need another $100,000 worth of fuel cells to make it stable enough as a primary and single source of energy.”
Strategic hybrid
The hydrogen version has an estimated maximum range of 570 km and an average range of 428 km, to the electric version’s average of 170 km. The outer dimensions, motor characteristics and suspension are identical between the two though; the former simply uses hydrogen for back-up energy, much like the Gal-class submarine’s diesel generator.

“When the fuel cell is deployed it charges the battery in a strategic, gradual way, to maximise the value gained from what remains an expensive fuel,” Bennett explains.
“The cost of hydrogen will probably fall faster than the rise in the gravimetric energy density of batteries, but thermodynamically, hydrogen will always cost more than grid electricity – you can’t get 100% efficient electrolysers or fuel cells. And hydrogen isn’t optimal for all EVs: maybe around 20% of commercial road freight can be served by all-electric EVs, and as batteries improve that figure will grow.”
Tevva therefore anticipates using whatever energy storage technologies achieve the best balance between weight and cost. Bennett asserts that in line with the company’s philosophy, “passenger cars should always be all-battery, because for their use-case, all-battery works. In our case, it works to have the hydrogen as a back-up energy system, but not as a load-following one.
“I used to drive a hydrogen car where the fuel cell was load-following. You could hear the PEMFC’s compressors and cooling systems revving up and down as you drove, and instead of incurring the parasitic losses from all those transients we can set the truck’s fuel cell at its most efficient band, and optimise its efficiency and value.”
Bennett acknowledges that batteries and hydrogen have downsides, as well as countless ancillaries across cooling, safety and more. This has prompted r&d into areas of the truck such as predictive energy management systems – again, inspired by his submarine days – exploiting automation and AI to eliminate the burden on fleet managers.
By this approach, the hydrogen truck might activate its fuel cell at half of maximum power when an estimated 2 hours remains before it runs out of energy, and rev its fuel cell up to full power when within an hour of battery energy depletion.
“All our trucks are essentially battery-electric, but the world’s electricity grids and battery factories alone can’t decarbonise trucks yet – and trucks emit more carbon than the entire maritime and aviation sectors combined,” Bennett says. “That’s a really serious problem, and we can’t afford to be sluggish about addressing it.
“Meanwhile, hydrogen is advancing too. Right now, around 100 Mt of hydrogen are produced every year, most of which is grey hydrogen from fossil fuels, and with a tiny fraction used for energy. So I believe there will be massive investments in the near future in PEM fuel cells as well as networks of blue hydrogen from carbon capture and green hydrogen production from renewable energy hydrogen networks. That’s what will lower hydrogen’s costs and widen its availability.
“It’s been a serious challenge to get to where we are, but we don’t want to wait for battery technology and the grid to catch up with clean energy needs, especially when we have everything we need right now to replace carbon-emitting trucks with something much cleaner.”
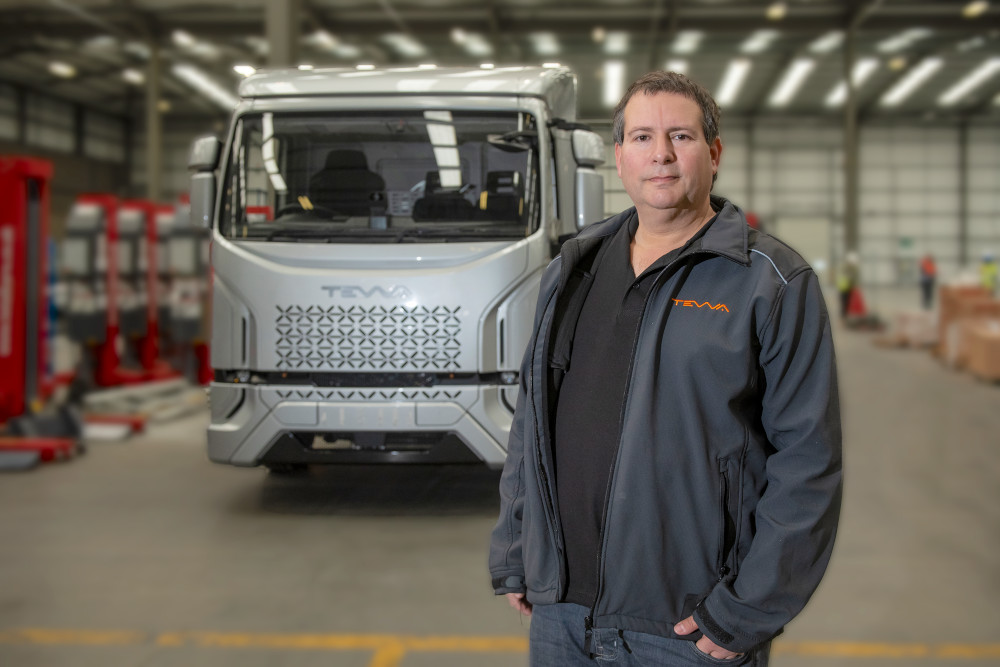
Asher Bennett
Asher Bennett was born and raised in Haifa, Israel, where he attended Carmel School primary and later Yavne College. After his secondary school education, he attended the Israeli Naval Academy, graduating and becoming a submarine officer in January 1990 for 4 years. After that, he studied at The International Institute for Management Development in Lausanne, Switzerland, where he attained his MBA.
In September 1998, he co-founded Coral-Tell, an internet software and services company, and was its CEO until 2002. During this time he also co-founded Yad2, which quickly became (and remains) one of Israel’s most successful e-commerce websites.
After 2002, he held different positions across software and venture capital firms, and in April 2008 became CEO of Evida Power, a developer and producer of battery packs and management systems for EVs. His time at Evida inspired him to found Tevva Motors in 2013, which he continues to lead as CEO at the company’s head office in Essex, England.
ONLINE PARTNERS
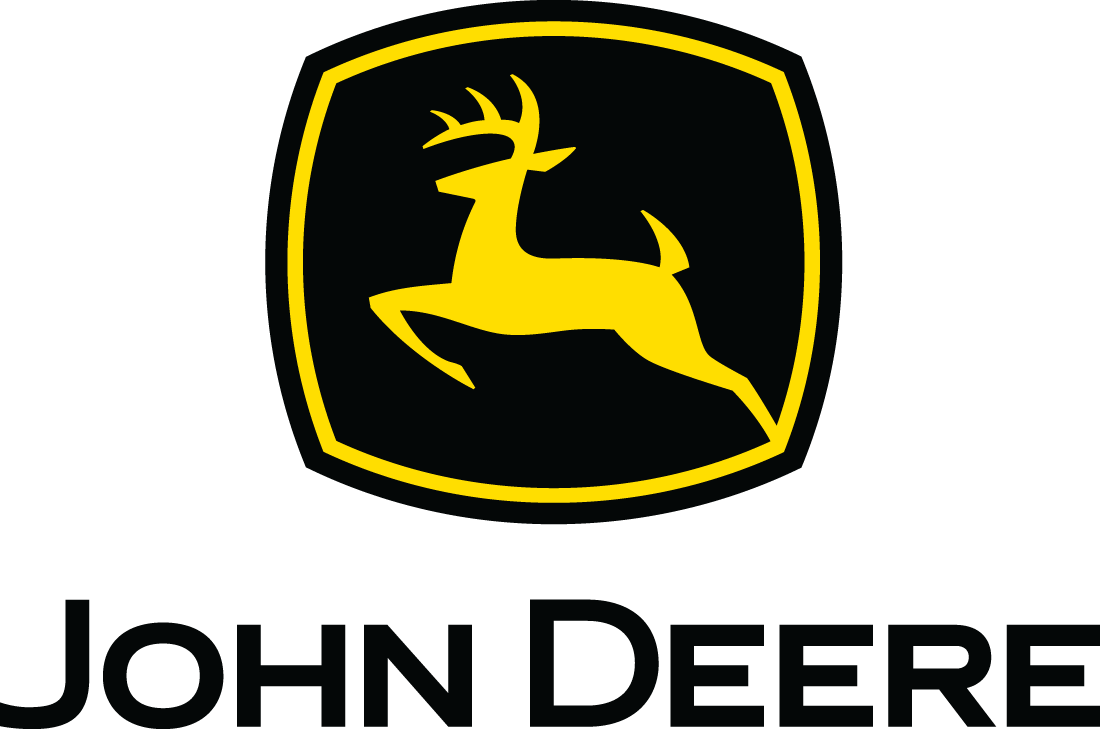
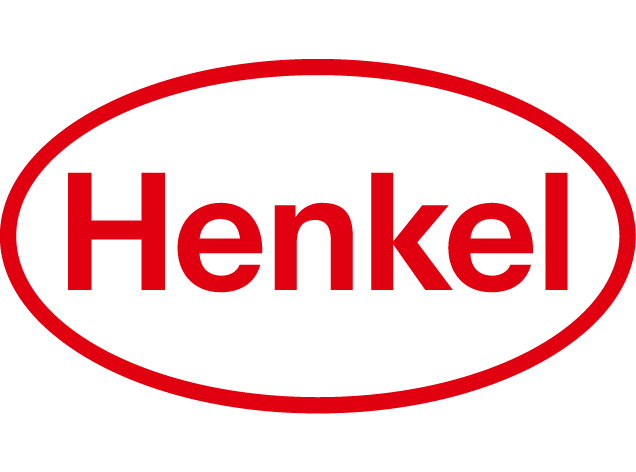
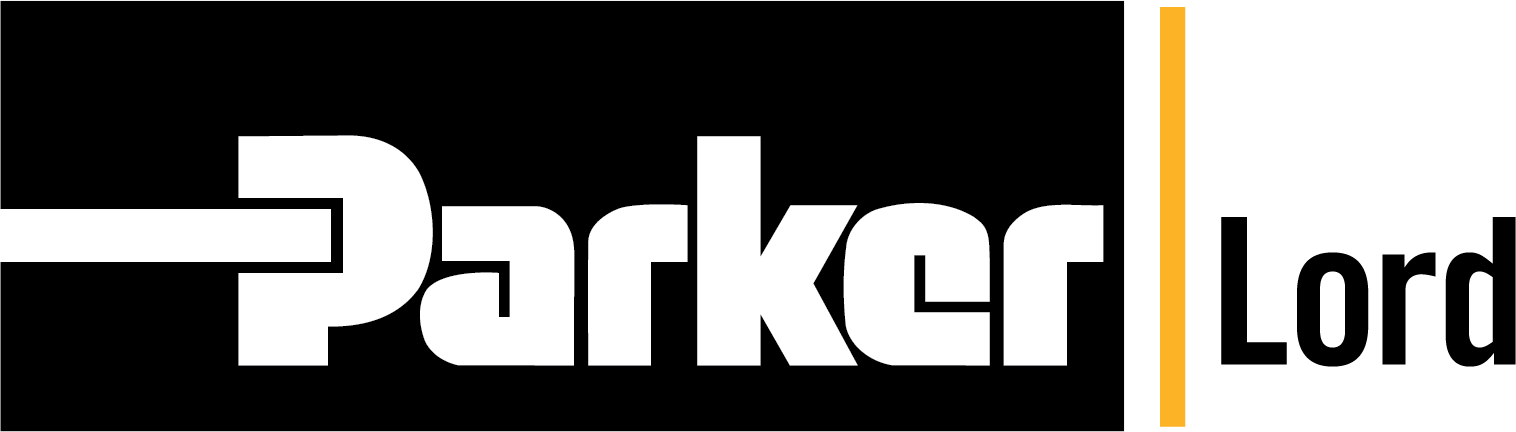
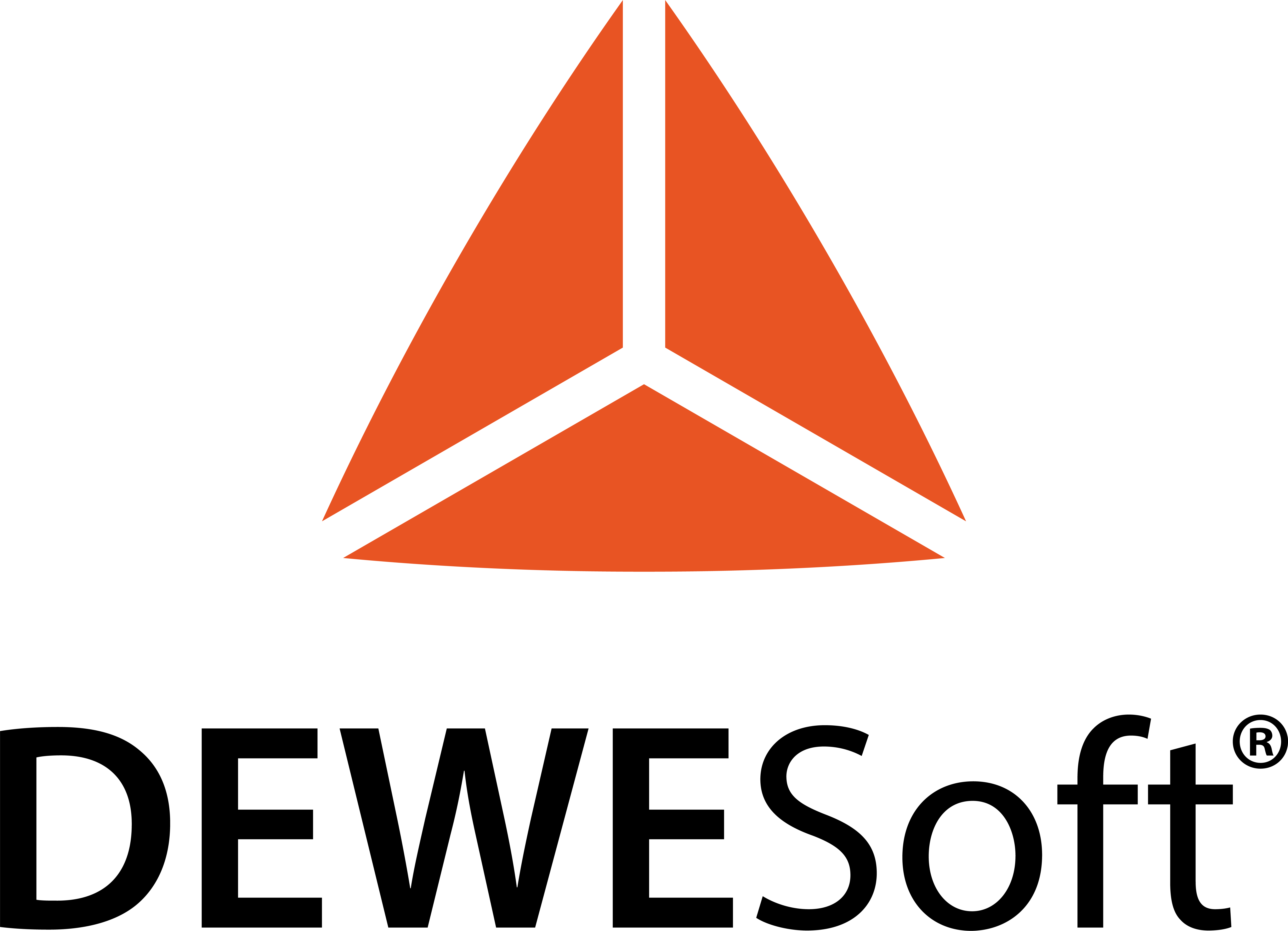
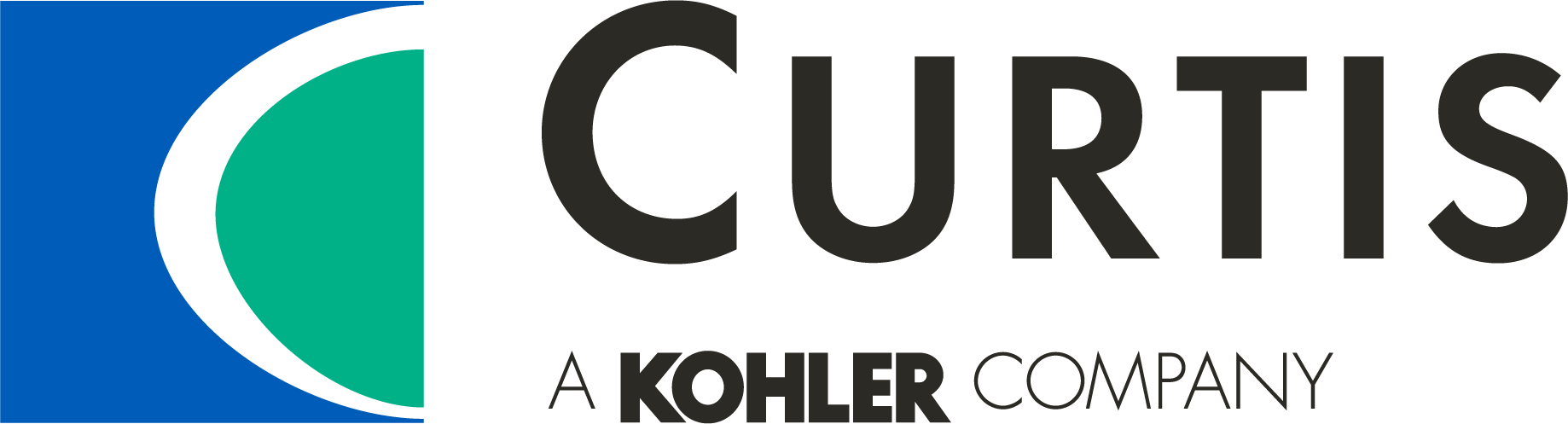
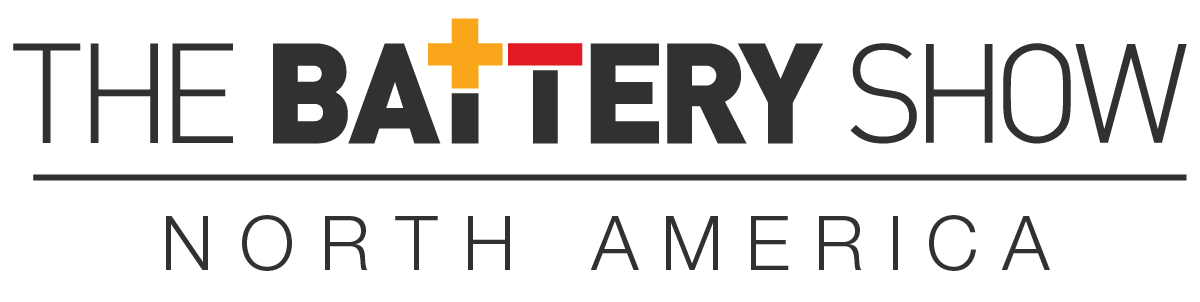
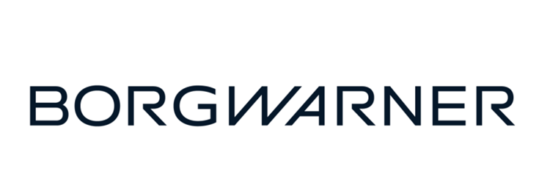